StörgrundanalyseBerechnung der Overall Equipment Effectiveness (OEE) mit der Störgrundanalyse
Mit der Kennzahl OEE Ausmaß der Störungen messen
Störungen bei Prozessen, Anlagen oder Maschinen wirken sich auf die Leistung des jeweiligen Prozesses aus. Die Leistung sinkt. In der Folge steigen die Prozesskosten, weil Reserven vorgehalten oder zusätzliche Kapazitäten zur Verfügung gestellt werden müssen, damit der geforderte Output des Prozesses erreicht wird. Das ist beispielsweise die Stückzahl in Produkten, die pro Tag hergestellt wird und die Qualitätsanforderungen erfüllt.
Die Kennzahl Overall Equipment Effectiveness (OEE) zeigt die tatsächliche Leistung eines Prozesses, einer Anlage oder einer Maschine im Vergleich zur theoretisch möglichen, maximalen Leistung.
Sie ist so definiert, dass gleichzeitig sichtbar wird, welchen Anteil die unterschiedlichen Störungen und Störarten auf die Leistung haben können. Denn die OEE berechnet sich aus drei einzelnen Faktoren: Anlagenverfügbarkeit, Leistungsgrad und Qualitätsrate.
Formel zu OEE: So berechnen Sie die Overall Equipment Effectiveness
Die Kennzahl Overall Equipment Effectiveness (OEE) misst den aktuellen Verfügbarkeits- und Wertschöpfungsstatus einer Anlage oder einer Anlagengruppe in der Produktion. Die OEE ist das Produkt aus drei Faktoren:
- Anlagenverfügbarkeit (AV)
- Leistungsgrad (LG)
- Qualitätsrate (QR)
Basis für die Berechnung ist die Planbelegungszeit einer Anlage. Die OEE ergibt sich aus der Multiplikation der drei Faktoren und wird meist als Prozentwert angegeben.
OEE = AV × LG × QR
Messung und Berechnung der Kennzahl OEE
Die Kennzahl OEE wird für einen definierten Prozess, eine Anlagengruppe, Anlage oder Maschine kontinuierlich gemessen. Grundlage dafür ist die Störgrundanalyse. Die einzelnen Störungen werden einem der drei Faktoren zur Berechnung der Overall Equipment Effectiveness zugeordnet. Aus der jeweiligen Zahl und Dauer der Störung wird dann die Kennzahl OEE berechnet.
In die Berechnung der OEE gehen unterschiedliche Parameter ein:
- Planbelegungszeit: Zeit (in Stunden) pro Tag oder Monat, in der die Anlage theoretisch eingesetzt werden kann, um den gewünschten Output herzustellen; maximal mögliche Nutzungszeit für die Anlage
- Produktionszeit: Zeit, in der die Anlage tatsächlich den Output liefert, für den sie gedacht ist – und in der sie nicht stillsteht oder wartet
- Stückzahl: Anzahl oder Menge des hergestellten Outputs in einem festgelegten Zeitraum; zum Beispiel pro Tag
- Geschwindigkeit: Zeitdauer, die die Anlage braucht, um eine Einheit des Outputs (ein Stück) herzustellen
- Qualität: Anteil des hergestellten Outputs (Stückzahl), der den Qualitätsanforderungen nicht entspricht – und deshalb aussortiert oder nachbearbeitet werden muss
Die Geschwindigkeit eines Prozesses oder einer Anlage kann beeinflusst werden durch technische Parameter (zum Beispiel Schnittgeschwindigkeit einer Fräsmaschine), durch äußere Einflüsse (zum Beispiel Temperatur, Material) oder durch das Leistungsvermögen des Mitarbeiters (zum Beispiel Schnelligkeit bei der Handhabung).
Außerdem spielen kleine Störungen wie „Zufuhr Teile klemmt“, „Tür nicht geschlossen“, „Datei lädt nicht“ eine Rolle.
Die Kennzahl OEE kann nur für bestimmte Prozesse und Anlagen sinnvoll berechnet werden. Zum einen müssen der Prozess oder die Anlage abgrenzbar sein; es muss klar angegeben werden, welche Aktivitäten betrachtet werden, wenn es um die Messung der Leistung geht. Zum anderen muss der Output zählbar oder messbar sein. Ein Output (Produkt) wird nicht nur einmalig erstellt, sondern in hoher Stückzahl (Serien- oder Massenproduktion).
Der Nutzungsgrad der Anlage sollte auch hinreichend groß sein. Die Leistung einer Anlage, die wegen fehlender Aufträge die meiste Zeit stillsteht, braucht in ihrer Leistung nicht verbessert zu werden. In der Praxis wird die Kennzahl OEE deshalb meist an Engpässen in einem Prozess ermittelt und analysiert.
Auswertung der Kennzahl OEE
Liegt die Overall Equipment Effectiveness für einen Prozess über 80 Prozent, wäre das Weltklasse; dieser Wert wird in der Praxis kaum erreicht. Ein OEE-Wert unter 65 Prozent gilt als Signal, dass der Prozess nicht rund läuft und häufig Störungen auftreten. Der Wert deutet darauf hin, dass es Verbesserungsmöglichkeiten im Prozess gibt und die Zahl und Dauer der Störungen hoch sind.
Liegt der Wert unter 30 Prozent, ist das ein Alarmsignal. Dabei muss aber auch die jeweilige Situation betrachtet werden: Art der Anlage, Reife und Komplexität des Prozesses, einmalige, besondere Ereignisse etc.
Ein direkter Vergleich der Kennzahl OEE zwischen unterschiedlichen Prozessen oder Anlagen ist problematisch, da jeweils andere Einflussfaktoren relevant sein können. Zum Beispiel Technologie oder die Art der Produkte. Meist wird die OEE für die Analyse und Bewertung im Zeitverlauf betrachtet. Änderungen deuten auf Probleme hin, die analysiert werden sollten.
Bevor Prozesse oder Anlagen allein aufgrund eines bestimmten OEE-Werts verändert werden, sollten also immer die im Einzelfall relevanten Rahmenbedingungen und die genauen Ursachen für den jeweiligen OEE-Verlauf analysiert werden. Es kommt darauf an, die genauen Störgründe zu identifizieren und deren Ursachen zu kennen.
Analyse der Störgründe nach OEE-Kategorien
In jedem Fall sollte bei niedriger OEE (unter 65 Prozent) geprüft werden, welche Störungen in der betrachteten Zeit aufgetreten sind und was die Störgründe und Ursachen waren. Hier setzt die detaillierte Störgrundanalyse an. Die Analyse der Störgründe orientiert sich dabei an den drei Faktoren, mit denen die OEE berechnet wird. Das sind:
Anlagenverfügbarkeit
Leistungsverluste ergeben sich dann, wenn die Anlage oder der Prozess stillsteht und nichts produziert. Das kann unterschiedliche Gründe haben. Störungen können beispielsweise sein:
- Anlage defekt
- Material fehlt
- Personal fehlt
- Anlage wird umgerüstet
- Anlage wird gewartet
- Anlage wird instand gesetzt, repariert
Wichtig ist dabei eine genaue Abgrenzung: Welche nicht-produktiven Zeiten sind geplant und welche resultieren aus ungeplanten Störungen? Beispiele für Stillstand einer Anlage, die geplant sind und deshalb nicht in die Minderleistung einbezogen werden, sind: Pausen oder Wartung. Ausnahme: Diese Zustände dauern länger als nötig und sollen dann gerade deshalb in die OEE-Berechnung und die Störgrundanalyse einbezogen werden.
Leistungsgrad
Eine Anlage oder ein Prozess sind so ausgerüstet, eingerichtet oder instruiert, dass sie in einer definierten Zeit eine definierte Menge des Outputs erzeugen sollten. In der Produktion wird die definierte Zeit als Zykluszeit bezeichnet. Das ist die minimale Zeit, in der im besten Fall ein Output erstellt wird, der keine Mängel oder Fehler hat.
Gegebenenfalls muss diese minimale Zeit, die bestmögliche Zykluszeit, experimentell bestimmt werden. Sie kann sich im Laufe der Zeit auch ändern – etwa durch technische Verbesserungen, Training des Bedienpersonals oder neue Technologien und Prozessverbesserungen.
In der Praxis muss diese Zykluszeit im Prozess gelegentlich erhöht werden. Es dauert dann länger als geplant, eine Einheit des Outputs zu erzeugen. Die Gründe dafür können sein:
- Einflüsse aus der Umwelt wie zu hohe Temperaturen, schlechtes Material oder falsche Einstellungen bei einer Maschine
- müde oder abgelenkte Mitarbeiterinnen und Mitarbeiter
- Mitarbeiterinnen und Mitarbeiter, die von Kollegen oder durch Anrufe unterbrochen werden
- Aufgaben, die schwieriger und langwieriger sind als gedacht
- kurze Stillstände (unter 5 Minuten) aus unterschiedlichen Gründen: Verstopfung, Magazin voll/ leer, Notstopp
Die Folge ist, dass ein Zyklus länger dauert als geplant. Der Leistungsgrad sinkt.
Qualitätsgrad
In der tatsächlichen Produktionszeit und mit der tatsächlichen Zykluszeit wird eine messbare Menge des Outputs hergestellt. Dieser Output kann allerdings einen Mangel oder Fehler haben. Er ist nicht in Ordnung. Maßgeblich sind die vorgegebenen Eigenschaften oder Merkmale des Outputs. An ihnen bemisst sich die Qualität.
Störungen können dazu führen, dass der Output (Produkte und Dienstleistungen) nicht den Qualitätsanforderungen genügt. Die entsprechenden Teile werden durch Qualitätssicherung identifiziert und ausgesondert (oder nachbehandelt). So verringert sich die Menge an hergestelltem Output um die Menge, die nicht in Ordnung ist.
Ermitteln Sie für wichtige Prozesse, Anlagen oder Maschinen in Ihrem Unternehmen die Kennzahl Overall Equipment Effectiveness (OEE). Betrachten Sie dabei insbesondere solche Anlagen, die eine hohe Auslastung haben oder Engpass-Kapazität sind.
Nutzen Sie dazu die Ergebnisse der Störgrundanalyse sowie eine der folgenden Excel-Vorlagen.
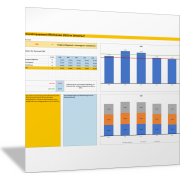
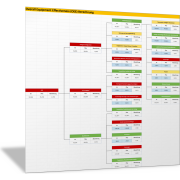
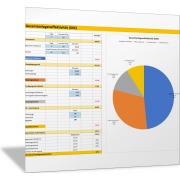
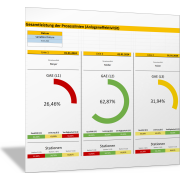