Fehler-Möglichkeiten- und Fehler-Einfluss-Analyse (FMEA)FMEA-Projekt vorbereiten und FMEA-Projektteam zusammenstellen
FMEA für Produkte und für Prozesse unterscheiden
Die Fehler-Möglichkeiten- und Fehler-Einfluss-Analyse (FMEA) ist eine wichtige Methode der vorbeugenden Qualitätssicherung. Sie trägt außerdem dazu bei, Risiken durch Produktfehler, die sich beim Kunden zeigen, einzugrenzen und zu vermeiden.
Schon bei der Produktkonzeption und beim Design, aber auch bei der Planung, Entwicklung und Konstruktion kann die FMEA zum Einsatz kommen; entsprechend wird zwischen Design-FMEA und Konstruktions-FMEA unterschieden.
Genauso wichtig ist eine FMEA bei der Prozessplanung in der Fertigung und der Montage, wo sie dann als Prozess-FMEA bezeichnet wird. Die FMEA kann zudem helfen, Qualitätsmängel in der Logistik oder bei Wartung und Instandhaltung zu vermeiden.
Für jede FMEA müssen Sie zunächst die Grundlagen schaffen und Vorbereitungen treffen. Die FMEA wird dann in den jeweiligen Prozessen verankert und regelmäßig durchgeführt. Die folgenden Schritte sind Teil der Vorbereitungen zur Durchführung einer Fehler-Möglichkeiten- und Fehler-Einfluss-Analyse.
FMEA-Projekte auswählen und abgrenzen
Anwendungsbereich abgrenzen
Gerade weil die Anwendungsmöglichkeiten sehr vielfältig sind, ist es im ersten Schritt erforderlich zu bestimmen, für welchen Bereich und für welchen Zweck die FMEA durchgeführt werden soll. Häufig wird in diesem Zusammenhang auch vom FMEA-System gesprochen; es umfasst alle relevanten Teilprodukte, Komponenten, Teilprozesse oder einzelne Abläufe, die eng miteinander zusammenhängen und über das System gekoppelt sind.
Der Anwendungsbereich muss klar abgegrenzt und erläutert werden. Mögliche Bereiche und Zwecke sind:
- Produkte oder Kundenlösungen werden in der Planungs- und Entwicklungsphase auf Fehlermöglichkeiten überprüft.
- Teile und Komponenten für bestehende Produkte werden überprüft, weil sich dort hohe Fehlerquoten gezeigt haben.
- Kritische Fertigungsprozesse, die kostenintensiv sind, werden überprüft, um Fehlermöglichkeiten zu reduzieren und Kosten für Nacharbeit zu senken.
- Montageprozesse werden überprüft, um Abläufe zu verbessern und mögliche Fehler zu vermeiden.
- Dienstleistungs- und Serviceprozesse werden im Hinblick auf Kundenzufriedenheit überprüft, um mit Schulungen Mängel in der Beratung zu beseitigen oder um geeignete Hilfsmittel zur Verfügung zu stellen.
Informationen zusammenstellen
Dann können die erforderlichen Informationen zusammengestellt werden. Diese sollten ausführlich beschreiben, wie das Produkt aufgebaut ist oder wie der Prozess abläuft. Wichtig sind vor allem:
- technische Pläne und Zeichnungen
- Lastenhefte
- Datenblätter
- Stücklisten
- Produkt- oder Prozessbeschreibungen
- Fotos oder Videos vom System
- Betriebsanleitungen und Handbücher
- Protokolle von Begehungen oder Besichtigungen
- Ergebnisse von Tests
- Ergebnisse von Sicherheits- und Gefährdungsprüfungen
- Musterteile
- fehlerhafte Teile
- ähnliche Produkte oder Betriebsmittel
- Kundenreklamationen
Normative Vorgaben kennen und beachten
Im Rahmen der Informationsrecherche müssen auch Gesetzestexte, Verordnungen, relevante Normen und Regeln der Technik herangezogen werden. Das ist besonders im Hinblick auf Mängelgewährleistung und Produkthaftung wichtig. Hier ist die FMEA ein Instrumentarium, um Sorgfaltspflicht und Verkehrssicherungspflichten nach dem Stand der Technik zu dokumentieren und sicherzustellen.
Oft machen die Kunden (zum Beispiel in der Automobilindustrie) konkrete Vorgaben, wie die FMEA im Unternehmen eingesetzt und verankert werden soll. Das kann beispielsweise in Qualitätssicherungsvereinbarungen vertraglich festgelegt werden.
Perspektive und Zielgruppe beschreiben
Hilfreich für die Identifikation und Analyse von Fehlermöglichkeiten und Fehlereinflüssen ist zudem, wenn die Perspektive benannt und beschrieben wird, aus der die Produkte und Prozesse betrachtet werden. Das sind meistens die Kunden, die das Produkt später nutzen, oder die Mitarbeiter, die im Prozess arbeiten oder die in die logistische Kette eingebunden sind. Diese sind die Zielgruppe der FMEA. Sie legen die Anforderungen fest, aus denen sich die einzelnen Qualitätsmerkmale ableiten und die dann mit der FMEA überprüft werden.
Zeitpunkt für die Durchführung der FMEA bestimmen
Erst wenn alle Informationen zum Produkt, zu den Produktkomponenten, zum Prozess und den eingesetzten Betriebsmitteln und Ressourcen vorliegen, kann eine FMEA durchgeführt werden. Alle, die an der Analyse beteiligt sind, müssen sich aufgrund dieser Informationen ein hinreichend gutes und genaues Bild vom Untersuchungsgegenstand machen können.
Um den richtigen Zeitpunkt zur Durchführung einer FMEA zu erkennen, können folgende Hinweise hilfreich sein:
Eine erste FMEA für ein Produkt sollte vor der Fertigstellung des Produktkonzepts durchgeführt werden. Sie kann im Verlauf der Planung, der Konstruktion und des Prototypenbaus angepasst und verbessert werden.
Die FMEA für einen Prozess sollte vor oder während der Durchführung von Machbarkeitsuntersuchungen und vor der Erstellung von Serienwerkzeugen gestartet werden.
Eine FMEA sollte immer dann durchgeführt werden, wenn Produkte oder Prozesse umfassend geändert werden oder wenn neue Erkenntnisse über den Anwendungsbereich vorliegen.
Grundsätzlich gilt: Eine FMEA sollte so früh wie möglich durchgeführt werden. Dabei muss dies kein einmaliges Ereignis sein. Im Gegenteil: Oft empfiehlt es sich, sie als iterativen Prozess während der Konzeptions- und Entwicklungsphase zu begreifen. Und auch beim Testen, bei der Bemusterung und bei der Prototypenentwicklung kann sie eingesetzt werden.
Zu beachten ist: Je später eine FMEA durchgeführt wird, umso teurer werden notwendige konstruktive Änderungen.
Wer am FMEA-Projekt teilnehmen sollte
Eine FMEA wird meist in der Form eines Projekts durchgeführt; deshalb auch die Bezeichnung FMEA-Projekt. Eine wichtige Grundlage für eine FMEA sind das Wissen und die Erfahrungen der Personen, die sie durchführen. Denn gerade bei der Identifikation und bei der Analyse von Fehlermöglichkeiten und Fehlereinflüssen oder Folgen ist technisches und Anwendungswissen notwendig. Zudem wissen erfahrene Mitarbeiterinnen und Mitarbeiter, wo in der Vergangenheit bereits Fehler aufgetaucht sind und was dafür Ursachen waren.
Fachexperten
Deshalb sollten alle Mitarbeiterinnen und Mitarbeiter eingebunden werden, die sich mit dem Produkt oder dem Prozess auskennen; sie bilden das FMEA-Team. Wichtig können sein:
- Entwickler
- Konstrukteur
- Test-Ingenieur
- Qualitätsmanager
- Fertigungsplaner
- Betriebsmittelplaner
- Prüfplaner
- Meister
- Werker
- Kunde
- Lieferant
Aufgabe der Mitarbeiter, die an der Durchführung beteiligt sind, ist eine Identifikation und Bewertung möglicher Fehler, die Analyse der Ursachen und die Einschätzung des Risikos. Um das aus unterschiedlichen Perspektiven qualifiziert tun zu können, ist es förderlich, wenn sich das FMEA-Team aus Mitarbeiterinnen und Mitarbeiter unterschiedlicher Fachabteilungen zusammensetzt.
Moderator
Besonders wichtig ist, dass sich alle Beteiligten gegenseitig für kompetent erachten und sich als Experten auf dem jeweiligen Feld respektieren. Das ist auch die Aufgabe des Moderators, der die Workshops plant und durchführt. Er sollte sich mit der Vorgehensweise der FMEA sehr gut auskennen, sicherstellen, dass die Methode richtig eingesetzt wird, und auf eine gute Zusammenarbeit im Team achten.
Konsequente Durchführung der FMEA sicherstellen
Schon im Vorfeld sollten die kritischen Erfolgsfaktoren beachtet werden. Wenn die FMEA nur sporadisch und halbherzig eingesetzt wird, wird sie als Werkzeug des Qualitätsmanagements irgendwann einschlafen. Nur die konsequente und regelmäßige Anwendung bringt die Erfolge. Es ist besonders zu beachten, dass die FMEA ernsthaft und gewissenhaft durchgeführt wird.
Zudem sollten die Erkenntnisse aus der FMEA-Analyse anschließend umgesetzt werden. Das heißt: Produkte müssen konstruktiv verbessert werden und Prozesse müssen technisch angepasst werden, wenn die Ergebnisse der FMEA das aufzeigen. Die möglichen Fehler und Mängel müssen durch Produktanpassungen und Prozessveränderungen beseitigt oder die Wahrscheinlichkeit ihres Eintretens minimiert werden.
Das funktioniert nur, wenn die verantwortlichen Manager, Produktmanagement, Produktentwicklung, Konstruktion, Leiter Fertigung oder Prozessmanager, persönlich das FMEA-Projekt initiieren und dann immer wieder ihre Unterstützung bieten. Sie müssen den Einsatz vorantreiben. Zudem müssen die Mitarbeiterinnen und Mitarbeiter in jedem FMEA-Team konstruktiv zusammenarbeiten und nicht Konflikte in die Teamarbeit hineintragen.
Projektleitung und Moderation brauchen FMEA-Erfahrung
Hilfreich ist, wenn eine Person für die Durchführung der FMEA verantwortlich ist; sie sollte mit der Methode und dem Ablauf einer FMEA vertraut sein. Die Durchführung kann wie ein Projekt organisiert werden. Deshalb die Bezeichnungen: FMEA-Projekt, FMEA-Projektleitung und FMEA-Team. Für die Teambesprechungen kann es hilfreich sein, zusätzlich einen Moderator einzusetzen, der mit der Methode und dem Ablauf der FMEA ebenfalls vertraut ist.
Fragen zur Vorbereitung einer FMEA klären
Klären Sie vor der ersten Durchführung einer Fehler-Möglichkeiten- und Fehler-Einfluss-Analyse (FMEA), ob die notwendigen Voraussetzungen geschaffen sind. Dazu sollten Sie folgende Aspekte klären und schriftlich dokumentieren:
- Was genau wollen Sie mithilfe der FMEA analysieren? Benennen Sie Produkte, Komponenten, Prozesse oder Systeme.
- Welche Ziele und Zwecke verfolgen Sie mit der FMEA? Was genau soll sich verbessern? Was soll minimiert, ausgeschlossen oder überwacht werden?
- Legen Sie Kennzahlen fest, anhand derer Sie später erkennen können, ob die FMEA die erwarteten Erfolge zeigt.
- Welche Standards oder Anforderungen in Ihrer Branche in Bezug auf Produktqualität, Produktsicherheit, Produkthaftung etc. müssen Sie beachten?
- Welche speziellen Anforderungen haben Kunden oder andere Stakeholder an Ihre Produkte und Prozesse?
- Welche Anforderungen und Rahmenbedingungen leiten sich daraus an die Durchführung der FMEA ab? Zum Beispiel spezielle Dokumentationspflichten oder Vorgehensweisen?
FMEA-Projektteam zusammenstellen und Projekt starten
Wenn Sie diese Fragen vorab geklärt und die Informationen zusammengestellt haben, sollten Sie die Durchführung der FMEA wie ein Projekt vorbereiten, planen und durchführen. Klären Sie insbesondere:
- Welche Mitarbeiterinnen und Mitarbeiter sollen ins Projekt-Team eingebunden werden?
- Was sind die Rahmenbedingungen für das Projekt und wie sieht der Zeitplan aus?
- Definieren Sie Projektziele und Projektergebnisse, die Sie erwarten.
Stellen Sie vor allem sicher, dass Ihr FMEA-Projektteam interdisziplinär zusammengesetzt ist und dementsprechend aus unterschiedlichen Fachbereichen kommt. Außerdem sollten alle Beteiligten das notwendige Wissen und Erfahrungen zum Produkt und Prozess haben.
Ergänzen Sie die Fachkompetenz um eine Person, die Besprechungen und Workshops als Moderator leitet und die sich sehr gut mit der Methode FMEA auskennt. Und treiben Sie das FMEA-Projekt voran, indem eine verantwortliche Person aus der Leitung (Produktmanagement, Leitung Qualitätsmanagement, Entwicklung oder Produktion) als Machtpromotor mitwirkt.
Speziell für die Vorbereitung und Planung eines FMEA-Projekts können Sie die folgende Vorlage nutzen.
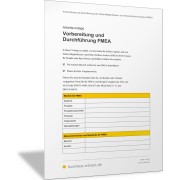
Im folgenden Abschnitt des Handbuch-Kapitels wird erläutert, wie eine FMEA aufgebaut ist (FMEA-Formblatt), wie Sie eine FMEA Schritt für Schritt durchführen und welche Instrumente und Werkzeuge Sie dabei einsetzen können.
„Fehler-Möglichkeiten- und Fehler-Einfluss-Analyse (FMEA)“ kaufen.