KaizenMethoden und Werkzeuge für Kaizen
Wofür Kaizen-Methoden einsetzen
Die Methoden und Werkzeuge, die für Kaizen angewendet werden, helfen zu erkennen, was verbessert und wie verbessert werden kann. Sie machen Ursachen von Fehlern oder Verschwendung aller Art sichtbar. Außerdem sind sie hilfreich bei der Analyse von Prozessen und ihren besonderen Merkmalen.
Mithilfe der im Folgenden dargestellten Methoden und Werkzeuge schaffen Sie in Ihrem Unternehmen oder Arbeitsbereich Transparenz, und Sie erkennen, was im Alltag verbessert werden kann.
Viele dieser Methoden und Werkzeuge wurden in Japan im Rahmen des Qualitätsmanagements entwickelt und perfektioniert. Ihr wesentlicher Vorteil ist, dass sie vergleichsweise einfach in der Anwendung sind, aber große Effekte erzielt werden können.
Wichtig ist, dass die Methoden und Werkzeuge von allen Mitarbeitenden gekannt und regelmäßig eingesetzt werden.
Mit Kaizen-Workshops Verbesserungsvorschläge einbringen, besprechen und umsetzen
Regelmäßig setzen sich die Mitarbeiterinnen und Mitarbeiter eines Arbeitsbereichs mit ihren Vorgesetzten zusammen und besprechen, welche Probleme aufgetaucht sind und welche Maßnahmen zur Verbesserung durchgeführt werden sollen. Wichtige Themen für diese Besprechungen sind:
- betriebliche Abläufe, Doppelarbeit, unnötige Tätigkeiten
- Qualitätsprobleme und Fehler bei Produkten, Werkzeugen oder Maschinen
- Arbeitsplatzorganisation mit aufwendigem Suchen, Schmutz, umständlichem Greifen
- Termintreue oder Zeitverzug bei einzelnen Tätigkeiten und Abläufen sowie deren Ursachen
- fehlende vorbeugende Instandhaltung und dadurch bedingte Ausfälle oder Defekte an Maschinen und Werkzeugen
- Arbeitsmittel, Werkzeuge oder Anwendungsprogramme, die nicht funktionieren, nicht passen, umständlich oder missverständlich sind
- Rationalisierungen, mit deren Hilfe Abläufe einfacher oder schneller gemacht werden können
- Möglichkeiten, um Kosten für Energie, Material oder Personal einzusparen
- Verbesserungen in der Logistik, indem Transportwege verkürzt, transportierte Mengen erhöht, Lagerbestände abgebaut oder die Verfügbarkeiten von Materialien, Teilen oder Werkzeugen verbessert werden
- Fehlzeiten und Krankenstände reduzieren durch Maßnahmen zum Arbeitsschutz und zur besseren Ergonomie
- Ordnung und Sauberkeit am Arbeitsplatz erhöhen die Motivation und erleichtern das Finden von Gegenständen oder Informationen
- Verbesserung des Informationsflusses, indem alle Mitarbeitenden die Informationen haben, die sie für ihre Tätigkeiten brauchen
- schnellere Einarbeitung neuer Mitarbeiter durch klare Regelungen, Einlernhilfen oder Mentoren
Die mit diesen Themen und Beispielen verbundenen Probleme dürfen für Kaizen-Maßnahmen nicht zu komplex sein. Idealerweise lassen sie sich von den betroffenen Mitarbeiterinnen und Mitarbeitern selbst lösen.
Wichtig: Die Teammitglieder gehen vor Ort an den jeweiligen Arbeitsplatz und schauen sich die Situation genau an. Dort wird besprochen, wie die Situation im Sinne von Kaizen verbessert werden kann.
5A-Aktion planen – nach dem 5S-Prinzip
Bei der 5A-Aktion wird das direkte Arbeitsumfeld eines jeden Mitarbeiters von ihm selbst analysiert im Hinblick auf Verschwendung und unnötige Aktivitäten. Im Japanischen wird diese Vorgehensweise auch als 5S-Prinzip bezeichnet – nach den japanischen Begriffen, die alle mit dem Buchstaben „S“ beginnen. Das sind:
- Seiri: Entferne Unnötiges aus deinem Arbeitsbereich!
- Seiton: Ordne die Dinge, die nach Seiri geblieben sind!
- Seiso: Halte deinen Arbeitsplatz sauber!
- Seiketsu: Mache Sauberkeit und Ordnung zu deinem persönlichen Anliegen!
- Shitsuke: Mache 5S durch Festlegen von Standards zur Gewohnheit!
Die 5A-Aktion besteht entsprechend aus den folgenden fünf Elementen:
1. Aussortieren
Alle Arbeitsgegenstände, Materialien, Informationen oder Handbücher werden genau betrachtet und analysiert bezüglich der Fragen:
- Wofür ist dieser Gegenstand wichtig?
- Wird dieser Gegenstand in den nächsten 30 Tagen gebraucht?
- Welche Maßnahmen müssen durchgeführt werden, um ihn zu beseitigen?
Am einfachsten ist, die betroffenen Mitarbeiter und ihr Vorgesetzter gehen durch den jeweiligen Arbeitsbereich und markieren alle Gegenstände, die nicht benötigt werden, mit einem Aufkleber.
Im Anschluss daran können sie überlegen, was jeweils damit gemacht wird. Sie können besprechen, warum Sie diesen Gegenstand weiterhin aufheben müssen. Oder Sie entscheiden sofort, ihn zu beseitigen (regelkonform zu entsorgen).
2. Aufräumen
Alle Gegenstände, die regelmäßig benötigt werden, erhalten einen festen Platz. Dieser wird eindeutig markiert. Ein ausgeklügeltes und für alle verständliches Markierungssystem kann helfen, dass Abläufe besser und reibungslos funktionieren, weil die Gegenstände schnell gefunden werden.
Am einfachsten ist: Die Kontur des Gegenstands wird an dem Ort gezeichnet, an dem er aufbewahrt wird. Oder: Es wird ein Foto abgebildet oder eine Beschriftung angebracht.
3. Arbeitsplatz sauber halten
Alle Arbeitsgegenstände werden regelmäßig gereinigt. Dabei werden sie auch auf ihre Funktionsfähigkeit geprüft. Mögliche Fehler- oder Schadensquellen werden identifiziert und so weit wie möglich eliminiert oder ausgeschlossen.
4. Anordnungen zur Regel machen
Die ersten drei Aufgaben müssen zur Regel gemacht und von den Mitarbeitenden verinnerlicht werden. Dazu müssen alle gemeinsam mit ihren Vorgesetzten klären und verbindlich vereinbaren, wie sie die 5A-Aktivitäten kontinuierlich durchführen.
Jedes Team benennt einen Verantwortlichen, der die Durchführung, Umsetzung und Anwendung der Regeln überwacht.
5. Alle Punkte einhalten und ständig verbessern
Auch die Mitarbeitenden selbst, ihre Vorgesetzten und das Management überprüfen die Umsetzung der 5A-Aktivitäten und bewerten, wie diese im Betriebsalltag angewendet werden. Dabei kann der Wettbewerb zwischen den Teams im Unternehmen gefördert werden:
„Wer ist besser bei 5A (5S)?“
3-Mu-Checkliste
Um Quellen der Verschwendung zu entdecken oder Ursachen von Problemen aufzudecken, gibt es im Kaizen zahlreiche Checklisten und Werkzeuge, die bei der Analyse helfen sollen. Ein einfaches Beispiel ist die 3-Mu-Checkliste. Sie ist benannt nach drei japanischen Begriffen:
- Muda: Verschwendung
- Muri: Überlastung
- Mura: Abweichung von Standards oder Regeln
In diesen drei Kategorien wird systematisch nach den folgenden Quellen für Verschwendung oder nach Problemen gesucht (mit Beispielen):
- Mitarbeiter: fehlendes Wissen, schlechte Ausführung
- Technik: fehlerhaft, defekt
- Methode: unklar, unzureichend, Arbeitspläne fehlerhaft, Stücklisten unvollständig, Zeichnungen unverständlich oder fehlerhaft
- Zeit: Vorgaben unklar, zu knapp, Wartezeit, Verzögerung
- Möglichkeit: Gestaltungsspielraum unklar, zu eng
- Vorrichtungen und Werkzeuge: ungenügend, defekt, fehlen
- Material: fehlt, fehlerhaft, hohe Lagerbestände
- Produktionsvolumen: zu umfangreich, Überproduktion (die im Lager liegt und nicht mehr genutzt wird)
- Transporte: überflüssig, zu lange Transportwege (Gebäude, Einrichtungen, Anlagen nicht aufeinander abgestimmt, umständliche Prozesse)
- Umlauf: Bestände zu groß, Zu- und Abgänge nicht planbar
- Platz: nicht aufgeräumt
- Bewegungsabläufe: unnötig, kompliziert
- Art zu denken: keine Beachtung von Verbesserungen und Vermeiden von Verschwendung
6W-Checkliste und Varianten
Eine weitere Checkliste zur Analyse des Arbeitsbereichs und der Verbesserungspotenziale ist die 6W-Checkliste. Dort sind Fragen aufgeführt, die ebenfalls bei der genauen Analyse von Prozessen und Tätigkeiten helfen.
Grundlage sind die sechs Fragewörter: Wer? Was? Wo? Wann? Warum? Wie? Damit können unterschiedliche Fragen verbunden sein:
- Wer: Wer macht es? Wer macht es gerade? Wer sollte es machen? Wer kann es noch machen? Wer soll es noch machen?
- Was: Was ist zu tun? Was wird gerade getan? Was sollte getan werden? Was kann noch gemacht werden? Was soll noch gemacht werden?
- Wo: Wo soll es getan werden? Wo wird es getan? Wo kann es noch getan werden? Wo sollte es noch getan werden?
- Wann: Wann wird es gemacht? Wann wird es wirklich gemacht? Wann soll es gemacht werden? Wann kann es sonst gemacht werden? Wann soll es noch gemacht werden?
- Warum: Warum macht der Mitarbeiter es? Warum soll es gemacht werden? Warum soll es hier gemacht werden? Warum wird es zu diesem Zeitpunkt gemacht? Warum wird es so gemacht?
- Wie: Wie soll es laut Plan gemacht werden? Wie wird es wirklich gemacht?
Oft findet man Varianten dieser 6W-Checkliste; zum Beispiel als 7W- oder 8W-Checkliste mit weiteren W-Fragen. Zum Beispiel:
- Wieso: Wieso wird es nicht anders gemacht? Wie soll es gemacht werden? Kann diese Methode auch in anderen Bereichen eingesetzt werden? Wie kann es noch gemacht werden?
- Wie viele: Wie viel ist das? Wie viel kostet das? Wie viel sollte das kosten? Wie viel können wir sparen?
Es kommt nicht darauf an, solche Checklisten genauso zu verwenden, sie sind kein starrer Formalismus. Vielmehr können weitere Fragen helfen, Verbesserungspotenziale zu finden.
Ishikawa-Diagramm mit 4-M-Checkliste
Eine Methode zur Ursachenanalyse ist das sogenannte Ishikawa-Diagramm, das von Kaoru Ishikawa von der Universität Tokio erfunden wurde. Das Ishikawa-Diagramm ist auch als Fischgräten-Diagramm bekannt. Mit dieser Technik können Ursache-Wirkungsbeziehungen abgebildet und Fehlerquellen entdeckt werden.
Die Methode soll den Anwender dazu bringen, systematisch Faktoren zu identifizieren und zu beschreiben, die Ursache für ein Problem sind. Dort lassen sich meistens auch die Lösungen zur Beseitigung des Problems finden.
Mit dem Ishikawa-Diagramm kommt man also den tatsächlichen Ursachen auf die Spur, um sie an der Quelle zu beseitigen.
Das Ishikawa-Diagramm funktioniert so: Zunächst formulieren Sie das Problem, schreiben dies an den rechten Blattrand und ziehen eine horizontale Linie nach links. Dann werden die wichtigsten Ursachenbereiche bestimmt und über- und unterhalb der horizontalen Linie angeordnet.
Ursachenbereiche sind nach der 4-M-Checkliste:
- Mensch
- Maschine
- Material
- Methode
Im nächsten Schritt werden für diese Ursachenbereiche jeweils sichtbare, messbare oder denkbare Faktoren als Ursachen für das Problem festgehalten und wie Äste um den jeweiligen Ursachenbereich angeordnet. So entsteht eine „Fischgräte“ wie in der folgenden Abbildung.
Es gibt verschiedene Varianten des Ishikawa-Diagramms. Oft werden nicht nur vier Fehlerbereiche oder Fehlerquellen betrachtet, sondern weitere: Milieu (Umfeld, Umwelt), Management oder Messung (7-M-Checkliste).
Die folgende Abbildung zeigt ein Beispiel für das Ishikawa-Diagramm, um Probleme und Ursachen für die lange Prozessbearbeitungszeit zu finden und einzugrenzen.
5-Mal-Warum-Fragen
Die 4-M- oder 7-M-Checkliste zeigt zunächst jeweils nur mögliche Ursachenbereiche in Form von allgemeinen Kategorien auf. Die eigentlichen Ursachen werden diesen zugeordnet und können weiter untergliedert werden.
Kernfrage für jeden Bereich ist: Welche Ursache für das Problem lässt sich anführen mit Bezug auf Mensch, Maschine, Material, Methode.
Für dieses Hinterfragen hat sich das Werkzeug des „5-Mal-Warum-Fragens“ bewährt (siehe folgende Abbildung). Die Zusammenstellung der Ursachenkette erfolgt beispielsweise in einem Brainstorming oder bei der Beobachtung von Abläufen.
Gemba-Kaizen
Um Fehler wirklich zu erkennen und Lösungen zur Fehlerbeseitigung zu finden, ist es zwingend notwendig, an den Ort des Geschehens zu gehen. Das meint Gemba-Kaizen.
Die Regel lautet: Gehe dahin, wo der Fehler und die Ursachen vermutet werden! Schaue alles genau an! Ziehe dann deine Schlüsse, was verbessert werden muss!
Hilfreich ist, wenn man sich dabei Notizen macht, Fotos oder Videos analysiert. Außerdem müssen die Mitarbeiter, die dort arbeiten, befragt werden:
- Was fällt schwer?
- Wo passiert Verschwendung?
- Was kann verbessert werden?
Die Lösungen werden mit ihnen ebenfalls besprochen. Wieder direkt vor Ort.
Solche „Gemba Walks“ oder das „Management by Walking Around“ müssen zur Routine für das Management werden. Was direkt vor Ort beobachtet und geklärt werden kann, muss nicht mehr in Berichten aufgeschrieben werden. Das Berichtswesen lässt sich so verschlanken.
Wichtig ist, dass die Mitarbeitenden verstehen, dass Gemba Walks durch das Management nicht zur Kontrolle ihrer Leistung da sind, sondern dem Kaizen-Denken dienen.
Regelmäßig Team-Workshops für Kaizen durchführen
Planen Sie Themen für erste Workshops zur kontinuierlichen Verbesserung. Welche Probleme sind offensichtlich und könnten gelöst werden?
Besprechen Sie einmal wöchentlich mit Ihren Kolleginnen und Kollegen sowie mit Ihrem Vorgesetzten alle aufgetretenen Fehler oder Verbesserungsmöglichkeiten. Sobald ein Fehler auftaucht, Verschwendung erkannt wird oder Ideen für Verbesserungen entstehen, werden diese notiert und dann im Team-Workshop eingebracht und besprochen.
Anschließend werden auf dieser Grundlage so viele Verbesserungen wie möglich auch umgesetzt.
5A-Methode oder 5S-Prinzip
Machen Sie die 5A-Methode und das 5S-Prinzip zum gelebten Standard in Ihrem Unternehmen – an jedem Arbeitsplatz, für alle Mitarbeitenden, in allen Bereichen.
Nutzen Sie die folgenden Vorlagen. Hängen Sie die 5S-Prinzipien (Regeln) für alle Mitarbeitenden gut sichtbar in Ihrem Arbeitsbereich aus (siehe folgende Abbildung).

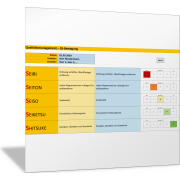
3-Mu-Methode
Nutzen Sie die folgenden Vorlagen und Checklisten, um Verschwendung, Überlastung und Abweichungen von Standards und Regeln durch falsche Aufgabendurchführung eines Mitarbeiters zu erkennen und zu beseitigen.
Nutzen Sie die Übersicht aus der folgenden Abbildung, um die sieben Arten der Verschwendung (7-Mu) zu erkennen und zu vermeiden. Sie können diese Übersicht in Ihrem Arbeitsbereich aushängen.
Mit den folgenden Vorlagen können Sie die Ursachen von Verschwendung, von Überlastung und von Regelabweichungen ermitteln und Lösungen zur Beseitigung finden.
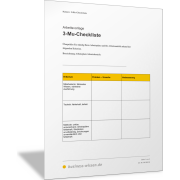

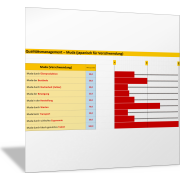
6W-Checkliste einsetzen
Überprüfen Sie Ihren Arbeitsplatz regelmäßig mit der 6W-Checkliste (oder auch der Variante mit weiteren Fragen).
Nutzen Sie dazu die folgende Checkliste und Vorlagen.
Nutzen Sie die Karte der folgenden Abbildung und hängen Sie diese in Ihrem Arbeitsbereich aus.
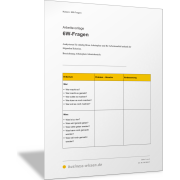
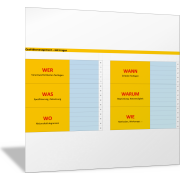
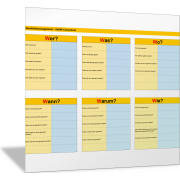
Ishikawa-Diagramm oder Fischgräten-Diagramm
Nutzen Sie das Ishikawa-Diagramm oder das Fischgräten-Diagramm (eine alternative Bezeichnung), um Fehlern und ihren Ursachen auf die Spur zu kommen.
Erkennen Sie mit den folgenden Vorlagen, welche Ursachen im Bereich Mensch, Maschine, Material, Methode, Milieu, Management oder Messung relevant sein können und machen Sie dies mit einem der folgenden Diagramme sichtbar.
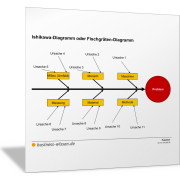
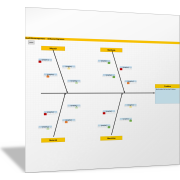
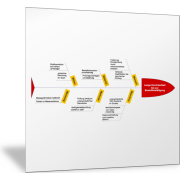

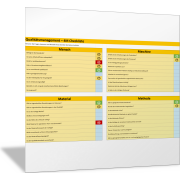
Nutzen Sie für die Ausarbeitung des Ishikawa-Diagramms die Methode des 5-Mal-Warum-Fragens. Vorlagen dazu sind:
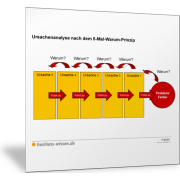
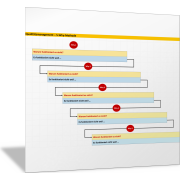
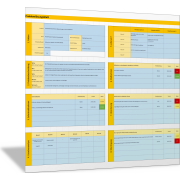
Die Checklisten und Arbeitsvorlagen wurden meistens in japanischen Produktionsbetrieben entwickelt. Teilweise müssen einzelne Kriterien auf die westliche Kultur übertragen werden.
Außerdem müssen Begriffe und Analysebereiche bei der Anwendung in Dienstleistungsbetrieben angepasst werden.
Kaizen lässt sich nicht von heute auf morgen im Unternehmen vorschreiben. Es muss in Form eines Change-Prozesses initiiert, vorangetrieben und verankert werden. Das Top-Management muss mit gutem Beispiel und mit Geduld vorangehen.