Ressourcen und Dienste planenMit SMED die Rüstzeit optimieren
Was bedeutet SMED?
Single Minute Exchange of Die (SMED) ist eine Methode, die im Rahmen des Lean Managements entwickelt wurde, um Rüstzeiten in Produktionsprozessen drastisch zu reduzieren. So soll der Wechsel eines Werkzeugs oder das Umrüsten einer Maschine weniger als zehn Minuten dauern.
Der Begriff stammt aus der Fertigungsindustrie und bezieht sich auf den Werkzeugwechsel in Bearbeitungsmaschinen; das sind beispielsweise Werkzeuge für das Umformen, Stanzen, Fräsen, Drehen oder Spritzgießen.
Die SMED-Methode wurde von Shigeo Shingo, einem der Mitbegründer des Toyota-Produktionssystems, entwickelt und wird vor allem in der Automobilindustrie sowie in anderen Fertigungsbranchen angewendet, wo häufige Umstellungen von Maschinen oder Anlagen nötig sind.
Was sind die Ziele von SMED?
Mit der SMED-Methode werden folgende Ziele verfolgt:
- Rüstzeiten reduzieren: Das Umrüsten von Maschinen soll vereinfacht und beschleunigt werden; damit verringert sich die Durchlaufzeit in der Produktion und Kunden können schneller beliefert werden.
- Flexibilität erhöhen: Durch kürzere Rüstzeiten können kleinere Losgrößen wirtschaftlicher produziert werden, was die Anpassung an Marktveränderungen oder Kundenwünsche erleichtert.
- Produktivität steigern: Weniger Stillstandszeiten bedeuten, dass Maschinen für die eigentliche Bearbeitung eines Werkstücks eingesetzt werden und wertschöpfend sind.
Vorteile von SMED
Die SMED-Methode bietet zahlreiche Vorteile, die Unternehmen helfen, ihre Produktionsprozesse effizienter und flexibler zu gestalten. Die wichtigsten sind:
- Kosteneinsparungen: Weniger Stillstandszeiten führen zu einer effizienteren Nutzung der Maschinen und geringeren Produktionskosten.
- schnellere Reaktionsfähigkeit: Produktionslinien können schneller an geänderte Anforderungen angepasst werden.
- weniger Überproduktion: Durch kürzere Rüstzeiten können kleinere Losgrößen produziert werden, was zu weniger Lagerhaltung und geringerer Verschwendung führt.
Die Phasen der SMED-Methode
Die Einführung der SMED-Methode erfolgt in mehreren Phasen, die Schritt für Schritt durchlaufen werden, um die Rüstzeiten einer Maschine zu minimieren. Jede Phase trägt dazu bei, den Rüstprozess technisch und organisatorisch zu verbessern.
Phase 1: Trennen von internen und externen Rüstvorgängen
In dieser Phase wird der gesamte Rüstvorgang detailliert analysiert und in zwei Kategorien unterteilt: interne und externe Rüstvorgänge. Interne Rüstvorgänge sind all jene Arbeiten, die nur dann durchgeführt werden können, wenn die Maschine stillsteht.
Ein Beispiel dafür wäre der Wechsel eines Werkzeugs, der nicht möglich ist, während die Maschine läuft. Diese internen Prozesse führen direkt zu Produktionsunterbrechungen und erhöhen die Stillstandszeiten.
Externe Rüstvorgänge hingegen sind Tätigkeiten, die bereits während des (noch laufenden) Produktionsprozesses erledigt werden können. Hierzu zählt beispielsweise das Bereitstellen von Werkzeugen, Materialien oder Auftragsunterlagen.
Ziel in dieser ersten Phase ist es, klar zwischen diesen beiden Arten von Rüsttätigkeiten zu unterscheiden. Die externen Tätigkeiten sollen so vorbereitet werden, dass sie parallel zur laufenden Produktion erledigt werden können. Dies reduziert die Zeit, in der die Maschine stillsteht.
Phase 2: Umwandlung interner in externe Rüstvorgänge
Nachdem in Phase 1 die Trennung von internen und externen Rüstvorgängen erfolgt ist, geht es nun darum, so viele interne Arbeiten wie möglich in externe zu verwandeln. Der Schlüssel liegt hier darin, Tätigkeiten, die traditionell nur während des Maschinenstillstands durchgeführt werden, so umzugestalten, dass sie bereits im Vorfeld (ganz oder teilweise) erledigt werden können.
Zum Beispiel könnte das Einrichten oder Einstellen von Werkzeugen oder das Vorbereiten von Materialien vor dem eigentlichen Maschinenstopp geschehen. Auf diese Weise kann die Maschine weiterlaufen, während die Vorbereitung bereits im Gange ist.
Diese Umwandlung erfordert oft organisatorische Anpassungen und möglicherweise auch Investitionen in zusätzliche Arbeitsmittel, um die parallele Vorbereitung zu ermöglichen. Der Nutzen ist jedoch erheblich, da jede Aufgabe, die vor oder nach dem Maschinenstopp erledigt wird, direkt zu kürzeren Rüstzeiten führt.
Phase 3: Optimierung der internen Rüstvorgänge
Die Rüstvorgänge, die sich nicht in externe Aufgaben umwandeln lassen und daher weiterhin während des Maschinenstillstands durchgeführt werden müssen, werden im nächsten Schritt so zeitsparend wie möglich gestaltet. Darum geht es in Phase 3.
Ziel ist es, die Zeit für diese Tätigkeit des Umrüstens an der Maschine zu minimieren. Dies geschieht durch verschiedene Ansätze, zum Beispiel durch technologische Verbesserungen, wie die Einführung von Schnellwechselvorrichtungen oder modularen Werkzeugen, die den Wechsel beschleunigen.
Zusätzlich helfen organisatorische Maßnahmen wie das Vereinfachen von Arbeitsschritten oder das Entfernen unnötiger Tätigkeiten, die internen Prozesse zu optimieren. Eine detaillierte Analyse jedes einzelnen Arbeitsschritts ist hier notwendig, um die Potenziale zu erkennen, das interne Rüsten zu beschleunigen.
Phase 4: Rationalisierung der externen Rüstvorgänge
Nachdem die internen Rüstprozesse optimiert sind, liegt der Fokus auf den externen Vorgängen. In dieser Phase wird sichergestellt, dass alle externen Rüstvorgänge nicht nur vor oder während des Produktionsprozesses erledigt werden, sondern auch so effizient wie möglich gestaltet sind. Dazu gehört beispielsweise:
- Vorbereiten und Bereitstellen von Werkzeugen in greifbarer Nähe
- rechtzeitiges Bereithalten aller benötigten Materialien
- frühzeitiges Überprüfen und Kalibrieren von Maschinenkomponenten
- optimierte Arbeitsplatzgestaltung mit genau festgelegten Bereichen für Werkzeuge, Materialien, Hilfsmittel etc.
- Übersicht und Ordnung am Arbeitsplatz
Dies stellt sicher, dass im Moment des Maschinenstillstands alle nötigen Werkzeuge und Materialien bereits vollständig vorbereitet und griffbereit sind.
Parallel zur laufenden Produktion werden diese externen Vorgänge kontinuierlich vorangetrieben, sodass im Idealfall keine Zeit verloren geht, wenn die Maschine für den Rüstvorgang angehalten wird. In dieser Phase ist auch der Einsatz von visuellem Management oder Checklisten zu empfehlen, um sicherzustellen, dass alle externen Tätigkeiten rechtzeitig und vollständig erledigt sind.
SMED im Unternehmen einführen
Um SMED in Ihrem Unternehmen erfolgreich einzuführen, ist ein strukturierter und praxisnaher Ansatz erforderlich, der speziell auf Ihre Produktionsprozesse abgestimmt ist. Ziel ist es, Rüstzeiten systematisch zu analysieren und zu reduzieren, ohne den laufenden Betrieb zu stören.
Im Folgenden ist Schritt für Schritt beschrieben, wie Sie dabei vorgehen.
Verständnis im Team schaffen
Bevor Sie mit der Einführung von SMED beginnen, ist es wichtig, dass alle Beteiligten das Konzept verstehen. Organisieren Sie Schulungen oder Workshops, um die Prinzipien von SMED zu vermitteln.
Stellen Sie sicher, dass Ihre Mitarbeitenden, insbesondere diejenigen in der Produktionsplanung, Disposition, Materialwirtschaft, Arbeitsvorbereitung, Fertigung, Montage und Instandhaltung, mit den Zielen und Vorteilen vertraut sind.
Anschauliche Beispiele nennen
Verwenden Sie reale Beispiele aus Ihrem Betrieb, um aufzuzeigen, wo es Engpässe gibt und wie die Reduktion der Rüstzeiten diese beheben könnte. Binden Sie Ihre Mitarbeitenden frühzeitig in den Prozess ein, damit sie die Relevanz erkennen und die Motivation zur Mithilfe steigt.
Pilotmaschine oder Pilotanlage wählen
Um SMED zunächst zu testen und die Ergebnisse zu validieren, analysieren Sie die Rüstvorgänge an ausgewählten Maschinen oder Anlagen. Wählen Sie eine Maschine oder Produktionslinie, bei der häufige Rüstvorgänge stattfinden, lange Rüstzeiten ein Problem darstellen und hohes Potenzial zur Reduzierung der Rüstzeit besteht.
Beginnen Sie mit einer Analyse des Rüstprozesses und der einzelnen Tätigkeiten. Dokumentieren Sie dabei sehr genau jeden Schritt und messen Sie die jeweilige Dauer.
Rüstvorgänge filmen
Filmen Sie den Rüstvorgang, um allen Beteiligten die Chance zu geben, den Prozess gemeinsam zu analysieren. Oft werden durch die visuelle Darstellung Verbesserungspotenziale sichtbar, die im Alltag übersehen werden.
Zwischen internen und externen Rüstvorgängen unterscheiden
Der nächste Schritt besteht darin, die verschiedenen Tätigkeiten während des Rüstvorgangs in interne und externe Arbeiten zu unterteilen.
- Interne Rüstvorgänge sind jene, die nur dann stattfinden können, wenn die Maschine stillsteht, wie zum Beispiel der tatsächliche Werkzeugwechsel.
- Externe Tätigkeiten, wie das Bereitstellen von Werkzeugen oder Materialien, können bereits im Vorfeld erledigt werden, während die Maschine noch in Betrieb ist.
Arbeiten Sie mit Ihrem Team daran, so viele interne Tätigkeiten wie möglich in externe umzuwandeln. Dies minimiert die Zeit, in der die Maschine nicht produziert.
Interne Rüstprozesse optimieren
Die verbleibenden internen Rüstvorgänge sollten so effizient wie möglich gestaltet werden. Überlegen Sie, wie die einzelnen Handgriffe und Arbeitsschritte vereinfacht, verkürzt oder parallelisiert werden können. Schnellwechselvorrichtungen oder standardisierte Werkzeuge sparen hier wertvolle Zeit.
Kaizen und Lean-Prinzipien integrieren
Integrieren Sie Kaizen und andere Lean-Prinzipien, wie 5S: Sparen, Säubern, Sortieren, Standardisieren und Selbstdisziplin. Schaffen Sie so Ordnung im Arbeitsbereich und verbessern Sie alle Rüsttätigkeiten kontinuierlich.
Optimierten Rüstprozess standardisieren
Sobald Sie den Rüstvorgang optimiert haben, ist es wichtig, den neuen Prozess zu dokumentieren und zu standardisieren. Erstellen Sie klare Arbeitsanweisungen oder Checklisten, damit alle Mitarbeitenden den neuen Ablauf befolgen.
Regelmäßige Schulungen und die Überprüfung der Einhaltung der Standards sind ebenfalls notwendig, um die Effizienz dauerhaft sicherzustellen.
Sorgen Sie dafür, dass die Verantwortlichen für die Rüstvorgänge regelmäßig Feedback geben und den Prozess weiter verbessern. Kleine Anpassungen können langfristig große Auswirkungen haben.
SMED auf andere Maschinen übertragen
Sobald Sie erste Erfolge mit einer Pilotmaschine erzielt haben, übertragen Sie das SMED-Konzept auf weitere Maschinen und Produktionslinien in Ihrem Unternehmen. Nutzen Sie die gewonnenen Erkenntnisse und Erfahrungen, um Rüstzeiten auch an anderen Stellen zu reduzieren und die Produktivität durchgängig zu steigern.
Arbeiten Sie iterativ – das heißt, Sie führen SMED Schritt für Schritt in Ihrem Unternehmen ein, um einen reibungslosen Übergang und messbare Verbesserungen sicherzustellen.
Beispiel: Betrieb führt SMED zur Rüstzeitoptimierung ein
Ein mittelständischer metallverarbeitender Betrieb stellt Bauteile für die Automobilindustrie her. In diesem Beispiel geht es um eine Fertigungslinie, die regelmäßig umgerüstet werden muss, um verschiedene Formen und Werkzeuge für die Produktion unterschiedlicher Bauteile zu verwenden.
Ausgangssituation
Das Unternehmen hat eine Stanzmaschine, die regelmäßig Werkzeuge wechseln muss, um verschiedene Metallteile für Automobilkunden herzustellen.
Bisher dauert der Rüstvorgang etwa 90 Minuten. Während dieser Zeit steht die Maschine komplett still, was die Produktivität mindert. Diese langen Rüstzeiten verursachen hohe Kosten, da die Maschine in dieser Zeit nicht produktiv ist.
Das Unternehmen ist dazu gezwungen, größere Produktionslosgrößen zu fahren, was wiederum zu höheren Lagerbeständen und mehr Kapitalbindung führt.
Zielsetzung
Das Unternehmen möchte die Rüstzeit auf unter 20 Minuten reduzieren, um die Flexibilität zu erhöhen und kleinere Losgrößen wirtschaftlich zu fertigen.
Ziele sind außerdem:
- die Maschinenverfügbarkeit zu steigern und
- die Umrüstzeiten drastisch zu senken, damit die Produktion flexibler auf Kundenanforderungen reagieren kann.
Hierbei ist das Unternehmen bereit, in Schulungen und technische Hilfsmittel zu investieren, um die Rüstprozesse zu verbessern.
Anwendung der SMED-Methode
Phase 1: Analyse und Trennung von internen und externen Rüstvorgängen
Im ersten Schritt beobachtet das Team den Rüstvorgang detailliert. Der komplette Wechsel wird gefilmt und in seine Einzelschritte zerlegt. Dabei stellt man fest, dass viele der Tätigkeiten, wie das Suchen und Holen der Werkzeuge, die Vorbereitung der Bauteile und das Kalibrieren der Maschine, während des Maschinenstillstands erfolgt. Sie werden intern durchgeführt.
Die Werkzeuge, die für den Wechsel benötigt werden, sind nicht direkt verfügbar. Der Maschinenbediener muss erst in das Lager gehen, um sie zu holen. Auch die Kalibrierung der Maschine geschieht erst, nachdem der Werkzeugwechsel abgeschlossen ist, was zusätzliche Zeit in Anspruch nimmt.
Phase 2: Umwandlung interner in externe Rüstvorgänge
Nach der Analyse wird damit begonnen, möglichst viele interne Vorgänge in externe zu verwandeln. Die Werkzeuge und Materialien, die benötigt werden, um das Rüsten durchzuführen, werden ab sofort im Voraus bereitgestellt.
Ein fahrbarer Werkzeugwagen wird eingeführt, der vor dem Maschinenstopp an den Arbeitsplatz gebracht wird. Das Rüstteam stellt sicher, dass alle nötigen Werkzeuge und Bauteile vor Beginn der Umrüstung bereitliegen, während die Maschine noch läuft. Außerdem wird das Team in der Anwendung eines Kalibrierungssystems geschult, das bereits während der laufenden Produktion vorbereitet werden kann.
Hierdurch ermöglicht das Unternehmen, dass mit dem Ende der Bearbeitung des vorangehenden Fertigungsauftrags sofort mit dem Umrüsten und dem Werkzeugwechsel begonnen werden kann. Das hat eine sofortige Reduktion der Maschinenstillstandszeit zur Folge.
Phase 3: Optimierung der internen Rüstvorgänge
Die verbleibenden internen Rüstvorgänge werden nun optimiert. Man stellt fest, dass der Werkzeugwechsel selbst noch viel Zeit in Anspruch nimmt, da die bisherige Befestigung der Werkzeuge mit Schrauben erfolgt.
Um diesen Prozess zu beschleunigen, wird in Schnellspannvorrichtungen investiert, die den Wechsel auf ein paar Handgriffe reduzieren. Zusätzlich wird das Personal für die exakte Abfolge des Rüstprozesses geschult und klare, standardisierte Arbeitsschritte werden festgelegt. Eine Checkliste sorgt dafür, dass nichts übersehen wird.
Durch diese Maßnahmen wird der Werkzeugwechsel von ursprünglich 45 Minuten auf 15 Minuten reduziert.
Phase 4: Rationalisierung der externen Rüstvorgänge
Die externen Rüstvorgänge, die nun bereits während der laufenden Produktion stattfinden, werden ebenfalls rationalisiert.
Ein weiterer Schritt zur Effizienzsteigerung besteht darin, eine feste Rüstverantwortung im Team zu etablieren. Es wird ein sogenannter Rüstkoordinator bestimmt, der sicherstellt, dass alle externen Vorbereitungen rechtzeitig und vollständig erledigt sind.
Die Werkzeuge werden jetzt an einem festen Platz in einem nahegelegenen Bereich gelagert, und es werden visuelle Management-Tools eingeführt, wie zum Beispiel Farbcodierungen und markierte Werkzeugplätze.
Ein weiterer Schritt zur Optimierung ist die Parallelisierung der Arbeiten. Beispielsweise wird die Maschine schon dann abgestellt, wenn zwei Teammitglieder parallel den Werkzeugwechsel durchführen können, während andere Mitarbeitende bereits die externen Arbeiten abschließen. Diese Arbeitsteilung verkürzt den Rüstvorgang weiter.
Ergebnisse
Nach der vollständigen Einführung der SMED-Methode ist es dem Unternehmen gelungen, die Rüstzeit der Stanzmaschine von ursprünglich 90 Minuten auf 18 Minuten zu reduzieren. Dies bedeutet eine enorme Produktivitätssteigerung, da die Maschine nun viel weniger Stillstandszeiten hat und länger wertschöpfend eingesetzt wird.
Zusätzlich wurde die Flexibilität erhöht, was es dem Unternehmen ermöglicht, kleinere Losgrößen zu fertigen, ohne dabei unwirtschaftlich zu arbeiten. Dies wiederum führt zu geringeren Lagerbeständen und einer besseren Reaktionsfähigkeit auf Kundenwünsche.
Die Einsparungen, die durch die Reduktion der Rüstzeiten erzielt wurden, machen sich sowohl in einer höheren Maschinenverfügbarkeit als auch in geringeren Kosten für Überstunden und unproduktive Zeit bemerkbar.
Gleichzeitig konnte die Produktion von 3000 auf 5000 Teile pro Tag gesteigert werden, da die Maschinenlaufzeiten erheblich verlängert wurden. Dies führt zu einer signifikanten Verbesserung der Liefertreue gegenüber den Kunden.
Anleitung und Checkliste zur Anwendung von SMED
Führen Sie die SMED-Methode systematisch und schrittweise an. Nutzen Sie dazu die folgende Anleitung mit Checkliste zur Unterstützung und Dokumentation.
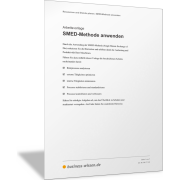
Mit Lean-Management Prozesse verschlanken
Lean-Management und Kaizen zielen darauf ab, Verschwendung zu minimieren und Prozesse effizienter zu gestalten. Die SMED-Methode unterstützt dieses Ziel, indem sie die Rüstzeiten in der Produktion drastisch verkürzt.
Mit der folgenden Vorlage wenden Sie die Lean-Grundsätze Schritt für Schritt an, um Ihre Prozesse langfristig zu verschlanken und gleichzeitig die Qualität zu verbessern.
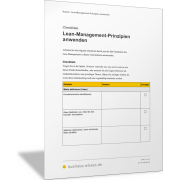
Maschinenstundensatz berechnen und Erfolg von SMED prüfen
Eine optimierte Rüstzeit wirkt sich positiv auf den Stundensatz Ihrer Maschinen aus. Mit der folgenden Vorlage berechnen Sie den Maschinenstundensatz genau – vor und nach der Anwendung der SMED-Methode. Die Kosten pro Stunde sollten für Ihre Maschinen mit optimiertem Rüsten mittel- und langfristig sinken, um wirtschaftlicher zu produzieren.
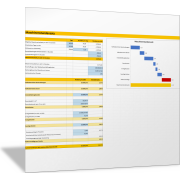
OEE: Wie produktiv arbeiten Ihre Maschinen?
Wie wirtschaftlich eine Maschine betrieben wird, ergibt sich letztlich aus mehreren Faktoren, die in der Kennzahl Overall Equipment Effectiveness (OEE) gemessen werden. Nutzen Sie die folgende Vorlage, um für die SMED-optimierte Maschine die Produktivität vor und nach Umsetzung der gewählten Maßnahmen zu vergleichen.
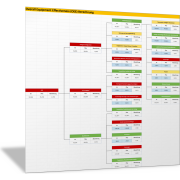