ProzessmanagementProzessanalyse – Schwachstellen in Prozessen erkennen
- Strategische Analyse der Kernprozesse und Hauptprozesse
- SWOT-Analyse
- Portfolio-Analyse
- Schwachstellen eines Prozesses erkennen
- Blindleistung erkennen und vermeiden
- Ursachenanalyse für Schwachstellen mit Ishikawa
- Beispiel: Prozessanalyse in der Bestellbearbeitung
- Rahmenbedingungen der Prozesse beachten
- 6 Vorlagen im Praxisteil
Strategische Analyse der Kernprozesse und Hauptprozesse
Da es kaum Prozesse ohne Schwachstellen geben dürfte, ist die Prozessanalyse eine kontinuierliche Aufgabe der Unternehmens- und Organisationsentwicklung. Allerdings ist es in der Praxis kaum möglich, alle Prozesse im Unternehmen im Blick zu haben und ständig so zu verändern, dass die Schwachstellen beseitigt werden.
Wichtig ist deshalb, dort anzusetzen, wo sich die schwerwiegendsten Probleme zeigen oder wo Verbesserungen die größten Effekte bringen. Die Auswahl der Prozesse, die genauer auf ihre Schwachstellen hin analysiert werden, basiert auf den Ergebnissen der Prozessmodellierung, der Leistungsindikatoren zur Prozessqualität und der Analyse der Prozesskosten.
Um „Kandidaten“ für eine genauere Prozessanalyse und Schwachstellenanalyse zu finden, ist ein hierarchisches Vorgehen hilfreich. Im ersten Schritt nimmt man die Kernprozesse eines Unternehmens unter die Lupe. Dafür gibt es zwei Herangehensweisen:
Herangehensweise an die Prozessanalyse – Variante 1
Es werden erst die übergeordneten Prozesse, Kernprozesse oder Hauptprozesse, identifiziert, modelliert, beschrieben und dann analysiert und bewertet. Später lassen sich untergeordnete Prozesse oder Teilprozesse im Detail betrachten. Dafür gibt es spezielle Prozessanalysten, die sich einzelne Prozesse herausnehmen und nach Schwachstellen suchen.
Herangehensweise an die Prozessanalyse – Variante 2
Es werden zunächst nur die wichtigsten Ziele und Erfolgsfaktoren als Bewertungskriterien genutzt, um die Prozesse grob zu „sortieren“. Ziele können sich beispielsweise auf Servicequalität, Durchlaufzeit oder Kosten beziehen.
Dann lassen sich für einzelne Prozesse spezielle Leistungsmerkmale formulieren und im Detail analysieren, um Schwachstellen und Verbesserungspotenziale zu finden. Hier sind die Prozessteams, also Führungskräfte und Mitarbeitende vor Ort (im Prozess) gefragt. Sie sollen Ihre Prozesse im Hinblick auf die Ziele analysieren und Schwachstellen beseitigen.
Im Folgenden werden einige Methoden und Herangehensweisen vorgestellt. Zunächst die SWOT-Analyse.
SWOT-Analyse
Die wichtigen Kernprozesse können zunächst einer SWOT-Analyse unterzogen werden. Hierbei geht es darum, die Stärken und Schwächen des Prozesses zu bestimmen (Strengths, Weaknesses) und anschließend die Gelegenheiten oder Chancen und Gefahren oder Risiken für die Zukunft abzuschätzen (Opportunities, Threats). Die folgende Tabelle zeigt, welche Fragestellungen dabei betrachtet werden.
Portfolio-Analyse
Ein weiteres Werkzeug der Prozessanalyse auf einer Ebene der übergeordneten Kernprozesse ist die Portfolio-Analyse. Dazu werden die Kernprozesse bezüglich zweier Vergleichsmerkmale in einer Matrix (Portfolio-Diagramm) abgebildet.
So kann ein Kernprozess mit folgenden Merkmalen beschrieben und im Portfolio-Diagramm dargestellt werden:
- strategische Bedeutung: gemessen an Beitrag des Prozesses zur Erreichung von wichtigen Zielen und zur Umsetzung von Strategien
- Verbesserungspotenzial: gemessen an Art, Umfang und Umsetzbarkeit von Maßnahmen zur Prozessverbesserung
Welche Prozesse miteinander verglichen werden, hängt vom Erkenntnisinteresse des Unternehmens ab. So lassen sich wichtige Kernprozesse wie Produktinnovation, Markteinführung, Produktion, Supply-Chain-Management (Materialbeschaffung), Vertrieb, Personalbeschaffung oder Kundenservice bezüglich ihrer strategischen Bedeutung und ihrem Verbesserungspotenzial vergleichen.
Genauso können Prozesse für einzelne Geschäftsfelder analysiert und in entsprechende Portfolios sortiert werden. Die folgende Abbildung zeigt ein mögliches Prozess-Portfolio für ausgewählte Kernprozesse eines Unternehmens.
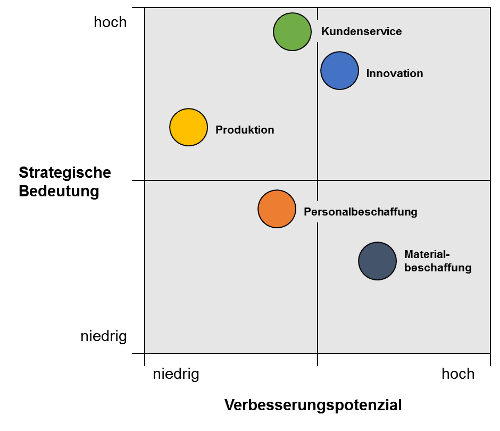
Schwachstellen eines Prozesses erkennen
Jeder Prozess kann bezüglich einer Vielzahl von Merkmalen und möglichen Schwachstellen analysiert und bewertet werden. Welche letztlich betrachtet werden, hängt von der übergeordneten Zielsetzung und den Ergebnissen aus der strategischen Prozessanalyse ab.
Im Allgemeinen lassen sich mögliche Schwachstellen in drei Kategorien einteilen – und in diesen Bereichen finden:
Prozessqualität
Hierunter fallen alle Schwachstellen, die dazu führen, dass der Prozess seinen Zweck nicht angemessen erfüllt und vorgegebene Ziele nicht erreicht werden. Meistens zeigen sich die Schwachstellen in hohen Fehlerraten, schlechter Ergebnisqualität (Ausschuss) sowie in Form von Störanfälligkeit oder Ausfallrisiken des Prozesses (häufige Unterbrechungen, hoher Wartungsaufwand).
Prozesszeit
Lange Durchlaufzeiten sind ein weiterer Indikator für Schwachstellen im Prozess. Die Durchlaufzeit ergibt sich aus dem Zeitbedarf für einzelne Prozessschritte wie beispielsweise Bearbeitungszeiten, Transportzeiten, Liegezeiten, Wartezeiten oder Rüstzeiten.
Ein weiterer Indikator kann die mangelhafte Termintreue sein, die beschreibt, ob das Prozessergebnis zum zugesagten Termin vorliegt; häufige Verspätungen sind ein Zeichen für Schwachstellen.
Prozesskosten
Hierunter fallen alle Kosten, die mit einem Prozess verbunden sind. Die Kosten hängen ab von: Personaleinsatz, Maschinen- und Anlageneinsatz, Fehlerraten, Effizienzgrade bei Energie- und Materialverbrauch, Wartungsbedarf oder Nutzung von Flächen und Einrichtungen.
Außerdem resultieren die Kosten aus den Leistungsmengen, die vom Prozess bewältigt werden müssen; oder aus der fehlenden Auslastung, wenn der Prozess auf höhere Leistungsmengen ausgelegt wurde.
Um Schwachstellen bei Qualität, Zeit und Kosten zu erkennen, brauchen Sie jeweils Merkmale und Indikatoren, an denen Sie die Leistung und den Ressourcenverbrauch Ihres Prozesses messen. Die Leistung und der Ressourcenverbrauch drücken sich meistens in Kennzahlen aus.
Weicht der Messwert einer Kennzahl von einer Zielvorgabe oder einem Sollwert ab, ist das ein Zeichen dafür, dass eine Schwachstelle oder ein Defizit im Prozess vorliegt – und es ein Verbesserungspotenzial gibt. Sie müssen für Ihren jeweiligen Prozess in jedem Einzelfall prüfen, welche Kennzahlen für die Identifikation und Analyse der Schwachstellen geeignet sind.
Blindleistung erkennen und vermeiden
Jeder Prozess hat einen bestimmten Zweck und soll vorgegebene Ziele erreichen. Der Teil eines Prozesses, der genau dafür sorgt, wird im Rahmen des Prozessmanagements als Nutzleistung eines Prozesses bezeichnet. Manche Teilprozesse sind dafür da, andere Prozesse zu unterstützen. Diese erbringen die sogenannte Stützleistung.
Kritisch sind solche Prozesse oder Prozessaktivitäten, die keine oder eine falsche Leistung erbringen; das sind die Blindleistung und Fehlleistung. Hier verbergen sich meistens Schwachstellen und es lassen sich wichtige Ansatzpunkte für die Prozessverbesserung ausmachen – etwa dadurch, dass unnötige Prozesse eingestellt werden.
Ursachenanalyse für Schwachstellen mit Ishikawa
Wer die Kennzahlen und Leistungsindikatoren eines Prozesses überprüft und wer sich außerdem den Prozess vor Ort anschaut und mit den Mitarbeitenden spricht, der kann die Schwachstellen – insbesondere die Symptome – meist schnell erkennen. Man erkennt zum Beispiel:
- Stapel und Warteschlangen
- überflüssige Informationen
- veraltete Informationen
- manuelle Nacharbeit
- häufige Rückfragen
- unklare Anweisungen
Die Ursachen und Gründe dafür sind nicht immer offensichtlich. Hier können mit einer Ursachen-Wirkungsanalyse die eigentlichen Mängel und damit das Optimierungspotenzial sichtbar gemacht werden.
Ein Werkzeug für die Ursachen-Wirkungsanalyse ist das sogenannte Ishikawa-Diagramm. Hier wird durch eine genaue Analyse des Prozesses, durch Auswertung von Dokumenten und Schwachstellen sowie durch Gespräche mit Mitarbeitenden ermittelt, worin die Mängel begründet sind. Nach Ishikawa-Methode gibt es folgende Fehlerquellen:
- Maschine: Die Technik, die im Prozess eingesetzt wird, funktioniert nicht zuverlässig.
- Mensch: Die Mitarbeiterinnen und Mitarbeiter sind nicht ausreichend qualifiziert oder sie sind unkonzentriert und engagieren sich nicht für die Ausführung der Aufgaben im Prozess. Es fehlt an Wissen, Erfahrung oder Konzentration.
- Material: Die eingesetzten Ressourcen, Werkstoffe, Material, Bauteile oder Informationen, sind mangelhaft, haben Fehler, sind unvollständig oder passen nicht.
- Methode: Die Anweisungen für die Durchführung des Prozesses sind nicht korrekt oder passen nicht zum Prozesszweck. Sie sind nicht auf die übergeordneten Ziele ausgerichtet. Oder der gesamte Prozess ist falsch konzipiert, indem die einzelnen Prozessschritte nicht aufeinander abgestimmt sind.
- Milieu (Umfeld): Die Rahmenbedingungen sind schädlich für den Prozessablauf. Ziele ändern sich ständig, es treten Störungen auf, Budgets sind zu knapp bemessen oder technische oder physikalische Einflüsse machen sich bemerkbar (Hitze, schlechte Luft, Lärm).
Mithilfe eines Ishikawa-Diagramms werden diese fünf Bereiche (5-M) genau betrachtet, und es wird nach entsprechenden Ursachen geforscht; durch Begehung, Hinschauen, Gespräche, Messungen – und ständiges Hinterfragen nach dem „Warum“.
Schließlich wird dies in einem Diagramm abgebildet, das wie in der folgenden Abbildung aussehen kann.
Beispiel: Prozessanalyse in der Bestellbearbeitung
Sie haben festgestellt, dass Kunden mehrere Tage auf die Bestellbestätigung warten müssen, wenn sie ein Produkt per E-Mail, Webseite oder Telefon bestellen. Dabei muss eine Bestellung von mehreren Personen geprüft werden. Unter anderem werden Preise kalkuliert sowie die Verfügbarkeit von Materialien und die technische Machbarkeit geprüft.
Ziel: hohe Kundenzufriedenheit durch schnelle Bestellbestätigung
Prozess: Bestellbestätigung mit Prüfung der Kundenbestellung durch die Abteilungen Technik, Materialwirtschaft, Produktmanagement und Controlling
Schwachstelle: Durchlaufzeit der Bestellbestätigung zu lang
Ursachenanalyse und Prozessanalyse mit der Ishikawa-Methode (Beispiele):
- Maschine: Es werden unterschiedliche EDV-Systeme für die Prüfungen eingesetzt; Daten müssen deshalb mehrfach erfasst und miteinander abgeglichen werden.
- Mensch: Mitarbeiter für die Prüfung der technischen Machbarkeit sind nicht ausreichend qualifiziert; müssen häufig in der Konstruktion nachfragen. Fehler bei der Prüfung kommen häufig vor und müssen nachgebessert werden.
- Material: Bestellungen durch Kunden sind nicht eindeutig, es muss beim Kunden nachgefragt werden. Prüfungsunterlagen sind nicht vollständig. Die Preiskalkulation basiert auf veralteten Daten.
- Methode: Technische und betriebswirtschaftliche Prüfung erfolgt an unterschiedlichen Standorten. Es gibt keine Arbeitsanweisungen für die technische Prüfung. Verfügbarkeitsprüfung im Lager erfolgt erst nach Abschluss der betriebswirtschaftlichen Prüfung.
- Milieu (Umfeld): Mitarbeiter der Bestellannahme arbeiten im Großraumbüro mit hohem Lärmpegel; dadurch gehen telefonisch eingegangene Informationen vom Kunden leicht verloren. Betriebswirtschaftliche Prüfungen dauern lange, da schlechtes Abteilungsklima (Streit unter Mitarbeitenden und Führungskraft).
Die folgende Abbildung zeigt diese Ursachen in der Übersicht im Ishikawa-Diagramm.
Rahmenbedingungen der Prozesse beachten
Gründe für einen nicht mehr funktionierenden Prozess können auch im Umfeld der Abteilung oder des Unternehmens liegen. Oft sind es Veränderungen am Markt, andere Kundenanforderungen oder Wettbewerber, die das Unternehmen zwingen, die Prozesse neu auszurichten.
Weitere Auslöser oder Ursachen können begründet sein in rechtlichen Änderungen oder neuen Techniken (EDV-System wurde geändert). Möglicherweise führt auch ein Wechsel der Geschäftsleitung, die andere Unternehmensziele verfolgt, dazu, dass Prozesse angepasst werden müssen.
Schließlich sind Prozesse darauf ausgerichtet, eine bestimmte Menge an Arbeit zu bewältigen. Wenn das Unternehmen erfolgreich ist und wächst, kann die Arbeit so zunehmen, dass sie mit den derzeitigen Prozessen nicht mehr zu schaffen ist.
Unternehmensprozesse und Kernprozesse strategisch bewerten
Identifizieren Sie die Kernprozesse in Ihrem Unternehmen, die Sie verbessern wollen, weil Sie dort viele Schwachstellen und hohes Verbesserungspotenzial vermuten. Hinterfragen Sie dazu:
- Was ist Anlass der Prozessanalyse?
- Welche Leistungsindikatoren legen nahe, dass ein Prozess nicht richtig funktioniert?
- Inwiefern ist dieser Prozess für Ihr Unternehmen von großer Bedeutung?
Bilden Sie Ihre strategische Einschätzung im Prozess-Portfolio für unterschiedliche Prozesse ab. Nutzen Sie dazu die folgende Vorlage.
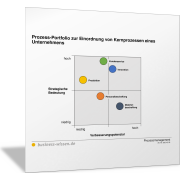
Mit den folgenden Excel-Vorlagen können Sie zudem automatisiert Portfolios für wichtige Prozesse darstellen in Bezug auf:
- Ressourcen und Ergebnisse
- Kundennutzen und Unternehmenserfolg
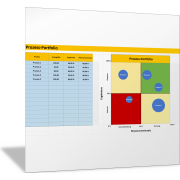
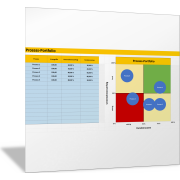
Operative Schwachstellen und ihre Ursachen im Prozess ermitteln und analysieren
Überprüfen und analysieren Sie die ausgewählten Prozesse auf Schwachstellen und ergründen Sie ihre Ursachen. Decken Sie Probleme auf und analysieren Sie diese. Erstellen Sie dazu mit der folgenden Vorlage ein Stärken-Schwächen-Profil für Ihren Prozess.
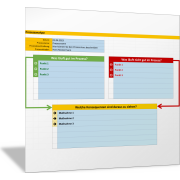
Bestimmen Sie anschließend Verbesserungspotenziale und den notwendigen Handlungsbedarf. Beachten Sie dabei insbesondere die Fehlerquellen:
- Maschine
- Mensch
- Material
- Methode
- Milieu
Nutzen Sie für die Ursachenanalyse das folgende Ishikawa-Diagramm.
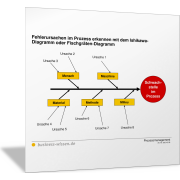
Mit der folgenden Excel-Vorlage können Sie Prozesse im Detail analysieren und die Anteile an den unterschiedlichen Leistungsarten (Nutzleistung, Stützleistung, Blindleistung und Fehlleistung) festhalten. So erkennen Sie kritische Schwachstellen und Ineffizienzen.
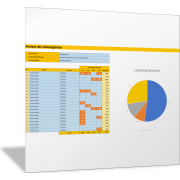
Diese genaue Analyse der Schwachstellen lohnt sich nur, wenn die erkannten Mängel und Probleme dann auch beseitigt werden. Erst dann werden die Prozesse verbessert. Manchmal genügen Prozessverbesserungen an wenigen, genau identifizierten Stellen; manchmal müssen Prozesse komplett neu geplant und gestaltet werden.