Fehler-Möglichkeiten- und Fehler-Einfluss-Analyse (FMEA)So führen Sie eine FMEA durch – Schritt für Schritt erklärt
Die Schritte der FMEA in der Übersicht
Die Durchführung einer Fehler-Möglichkeiten- und Fehler-Einfluss-Analyse (FMEA) erfolgt in mehreren Schritten. Je nachdem, auf welche Beschreibung zur FMEA Sie sich dabei beziehen, sind diese Schritte etwas anders eingeteilt und unterschieden. Die jeweiligen Aufgaben und Inhalte sind dabei meist ähnlich oder identisch.
Der Standard, der nach gemeinsamer Modellentwicklung durch die Automobilverbände VDA und AIAG definiert ist, sieht insgesamt sieben Schritte der FMEA in drei Phasen vor. Die Schritte sind:
- Planung und Vorbereitung: Identifikation und Definition des FMEA-Projekts; Abgrenzung des Produkts und des Prozesses
- Strukturanalyse: Struktur des Systems analysieren, das mit der FMEA betrachtet wird
- Funktionsanalyse: Zusammenstellung aller relevanten Produktfunktionen oder Prozessschritte
- Fehleranalyse: Identifikation möglicher Fehler, Erkennen von Fehlerketten, Fehlerursachen und Fehlerfolgen im Produkt oder Prozess
- Risikoanalyse und Maßnahmenanalyse: Erkennen und bewerten von Risiken und Folgen, wenn der Fehler entsteht und nicht rechtzeitig beseitigt wird; mögliche und notwendige Maßnahmen identifizieren
- Optimierung und Maßnahmenumsetzung: Festlegung von Maßnahmen zur vorbeugenden Fehlervermeidung, Umsetzung der Maßnahmen und kontinuierliche Verbesserungen am Produkt oder Prozess
- Ergebnis-Dokumentation: Kommunikation der Ergebnisse an die betroffenen Fachbereiche und Schlussfolgerungen aus der FMEA
Die Schritte 1 bis 3 sind der Phase „Systemanalyse“ zugeordnet, die Schritte 4 bis 6 der Phase „Fehleranalyse und Risikovermeidung“ und der Schritt 7 ist die Phase „Risiko-Kommunikation“.
In jedem einzelnen Schritt der FMEA-Durchführung muss das Projektteam eine Fülle von Fragestellungen und Aufgaben bearbeiten. Dabei können unterschiedliche Werkzeuge eingesetzt werden. Diese werden im Folgenden vorgestellt.
Planung und Vorbereitung: FMEA-Projekt definieren und starten
Im ersten Schritt wird festgelegt, was im Rahmen der FMEA genau betrachtet werden soll. Das kann ein Produkt, eine Komponente, ein Prozess oder ein Fertigungsschritt sein, genauso wie Abläufe beim Erbringen einer Dienstleistung oder bei überbetrieblicher Logistik. Konkret kann das FMEA-Projekt Teil sein von:
- Neuentwicklung eines Produkts
- Produktänderung
- Analyse von komplexen Herstellverfahren
- Gefahrenanalyse von sicherheitsrelevanten Produkten oder Prozessen
- Einsatz neuer Maschinen und Anlagen
- Analyse von Prozessen und Produkten mit hohem Umweltrisiko oder Risiken für den Arbeits- und Gesundheitsschutz
- Analyse von veränderten Einsatzbedingungen beim Kunden
Der Bereich und das Objekt, das mithilfe der Methode FMEA betrachtet werden soll, werden so eingegrenzt und beschrieben. Mit der Planung und Vorbereitung soll festgelegt werden, was im FMEA-Projekt betrachtet und analysiert werden soll – und was nicht. Damit wird auch abgesteckt, wie hoch die Eindringtiefe und Detaillierung der FMEA sein soll.
Daraus leitet sich der Projektauftrag ab. Mit ihm werden die Ziele des Projekts definiert, das Projektteam mit der Projektleitung und Moderation sowie der Projektsponsor festgelegt sowie ein Aufgabenplan und ein Zeitplan entwickelt.
Dieser Schritt endet mit einem FMEA-Kick-off-Meeting und einem Protokoll dazu.
Strukturanalyse
Mit der Strukturanalyse werden zunächst alle Elemente aufgelistet, die an dem Betrachtungsobjekt der FMEA (System, Produkt, Prozess etc.) beteiligt sind. Dazu wird das Gesamtsystem Schritt für Schritt in seine Einzelteile zerlegt. Unterscheiden lassen sich die Strukturanalyse für ein Produkt und für einen Prozess.
Strukturanalyse für ein Produkt
Ein Produkt lässt sich als System beschreiben durch: Teilsystem, Baugruppe, Bauteil, Komponente, Teil, Material und Merkmal, aus denen es besteht. Das lässt sich in eine hierarchische Darstellung mit mehreren Ebenen bringen, wie in Abbildung 1 dargestellt.
Strukturanalyse für einen Prozess
Eine solche Strukturanalyse lässt sich nicht nur für Produkte, sondern auch für Prozesse durchführen. Hier werden die Ebenen und die Elemente meist anders bezeichnet. Zum Beispiel: Hauptprozess, Teilprozess, Aufgabe, Tätigkeit, Betriebsmittel, Hilfsmittel, Arbeitsanweisung oder Durchführung. Oft wird dazu auch die Systematik des Ishikawa-Diagramms genutzt mit den Elementen:
- Mensch
- Maschine
- Material
- Methode
- Milieu
Schnittstellen und Funktionsweise des Systems
Mit der Strukturanalyse für Produkte und Prozesse wird herausgearbeitet, welche Schnittstellen es zwischen den Elementen eines Systems gibt und wie diese gestaltet sind. Schnittstellen können zwischen Elementen derselben, aber auch unterschiedlicher Stufen bestehen. Zudem kann es sich um technische Schnittstellen handeln, aber auch um organisatorische. So kann in der Darstellung sichtbar gemacht werden, wo die Schnittstelle zwischen Hersteller und Lieferant verläuft; interne und externe Elemente werden unterschieden.
Da die Strukturanalyse mit der Auflistung der Elemente, ihres Zusammenspiels und der Schnittstellen sehr umfangreich werden kann, kann das FMEA-Projektteam eingrenzen und abgrenzen. Es legt fest, bis zu welchem Detaillierungsgrad das System betrachtet wird und welche Schnittstellen von Bedeutung sein können, wenn es um Fehlermöglichkeiten geht.
Funktionsanalyse
Das System und seine einzelnen Elemente werden bezüglich ihrer Funktionen und Aufgaben beschrieben. Meistens hat ein Produkt eine Kernfunktion sowie weitere Nebenfunktionen. Die Kernfunktion sagt aus, wofür es das Produkt überhaupt gibt. Beispiele:
- Kugelschreiber für das Schreiben oder Malen auf Papier
- Flaschendeckel soll eine Flasche abdichten
- Motor soll Drehmoment erzeugen
Jede Funktion ist für die Gebrauchstauglichkeit und den Einsatz des Produkts wichtig. Die Bedeutung der einzelnen Funktionen ergibt sich aus der Anforderungsanalyse: Was will der Kunde oder Nutzer?
Die Funktionen eines Produkts lassen sich in einem Funktionsbaum darstellen. Dazu werden Kundenanforderungen daraufhin analysiert: Wie lässt sich diese Anforderung oder Funktion realisieren? So entstehen eine hierarchische Darstellung und ein Funktionsnetz, wie sie in Abbildung 2 am Beispiel eines Infusionsflaschenaufhängers dargestellt sind.
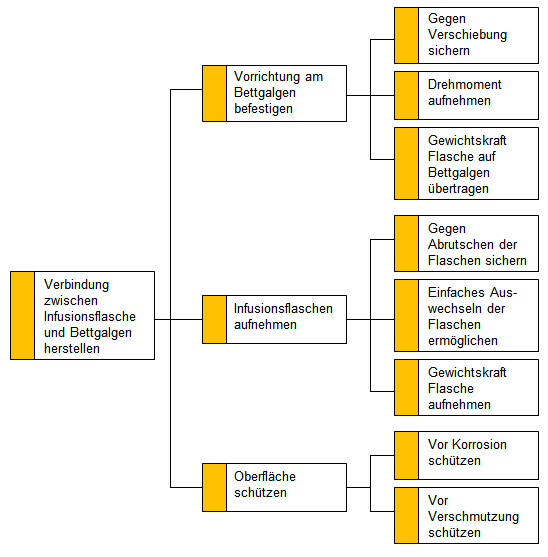
Mit der Funktionsanalyse lässt sich prüfen, ob das Produkt das leistet, was es soll. Dazu werden Messungen durchgeführt. So lässt sich das Lastenheft validieren.
Die Funktionsanalyse kann nicht nur für Produkte, sondern auch für Prozesse durchgeführt werden. Hier geht es darum zu beschreiben und zu prüfen, was einzelne Prozessschritte tun und bewirken und welchen erwünschten Output sie erzeugen.
Fehleranalyse
In diesem Schritt wird der Funktionsbaum oder das Funktionsnetz mit allen Funktionen des Systems daraufhin analysiert, welche Fehler, Schäden und Gefahren auftauchen können. Diese werden jeweils zu den Funktionen geschrieben und damit aufgelistet. Aus den Funktionen und den Aufgaben, die dieses System normalerweise erfüllen müsste, werden mögliche Fehler, Schäden, Gefahren oder Risiken (Fehlfunktionen) systematisch ermittelt.
Am Beispiel des Infusionsflaschenaufhängers aus Abbildung 2 können mögliche Fehler sein:
- Funktion: Vorrichtung am Bettgalgen befestigen
möglicher Fehler: Befestigung löst sich - Funktion: Vor Verschmutzung sichern
möglicher Fehler: Schmutz setzt sich in Ritzen fest
So werden mit der Funktionsanalyse sämtliche Funktionen hinterfragt und im FMEA-Projektteam besprochen, welche Fehler entstehen könnten. Fehler sind dadurch gekennzeichnet, dass die Funktion nicht erfüllt oder ausgeführt wird, dass sie schlecht oder nur teilweise ausgeführt wird oder dass sie unbeabsichtigt ausgeführt wird.
Jeder mögliche Fehler wird dann daraufhin geprüft, was die Fehlerursache sein kann und welche Folgen dieser Fehler haben kann. So entsteht ein Fehlernetz aus Fehlerbeschreibung, Fehlerursachen und Fehlerfolgen.
Mögliche Fehlerursachen und Fehlerfolgen lassen sich aus dem Diagramm der Systemanalyse und der Funktionsanalyse ableiten (siehe Abbildung 1 und Abbildung 2); denn dort sind die Zusammenhänge und Abhängigkeiten dargestellt. Fehlerfolgen ergeben sich meistens auf der hierarchisch höheren, Fehlerursachen auf der hierarchisch niedrigeren Stufe.
Schließlich lassen sich die Ergebnisse der Analysen in einem weiteren Diagramm zusammenfassen, wie es in Abbildung 3 schematisch dargestellt ist.
Risikoanalyse und Maßnahmenanalyse
Mit den möglichen Fehlern, Fehlerursachen und Fehlerfolgen kann das Risiko eingeschätzt und bewertet werden, das mit dem jeweiligen Fehler verbunden ist. Im Rahmen der FMEA wird dazu geklärt:
- Wahrscheinlichkeit des Auftretens des Fehlers und der Fehlerursachen (A)
- Bedeutung der Fehlerfolgen in Bezug auf Sicherheit, Kundenzufriedenheit, Kosten, Imageverlust etc. (B)
- Wahrscheinlichkeit, dass der Fehler entdeckt und rechtzeitig erkannt wird (E)
Mit diesen drei Faktoren wird die Risikoprioritätszahl (RPZ) berechnet nach der Formel:
RPZ = A x B x E
Diese Kennzahl bildet das „echte Risiko“ aber nur unzureichend ab. Denn bei dieser Berechnung hat ein hoher Entdeckungs-Wert (E) das gleiche Gewicht wie ein hoher Bedeutungs-Wert (B). Ein unbedeutender Fehler, der kaum entdeckt wird, führt zur gleichen RPZ wie ein sehr schwerwiegender Fehler, der vermutlich auch entdeckt wird.
Wichtig ist aber der zweite Fall: Schwerwiegende Fehler mit hoher Bedeutung müssen beseitigt werden; unbedeutende Fehler verlässlicher zu entdecken, ist weniger wichtig. Das Gesamtrisiko hängt also viel mehr von der Bedeutung, der Schwere der Folgen, ab als davon, ob der Fehler entdeckt wird oder nicht.
Action Priority
Daher wurde 2019 mit dem FMEA-Handbuch von VDA und AIAG eine neue Risiko-Bewertung eingeführt: die Aufgabenpriorität oder Action Priority (AP). Die Bewertung erfolgt damit in drei Stufen oder Klassen:
- High = Höchste Priorität für die Maßnahme: Es müssen vordringlich Maßnahmen gefunden werden, damit der Fehler nicht auftritt oder zumindest zuverlässig entdeckt wird. Sind keine geeigneten Maßnahmen möglich, muss begründet und dokumentiert werden, warum die bestehenden ausreichen.
- Middle = Mittlere Priorität für die Maßnahme: Es sollten Maßnahmen gefunden werden, damit die Wahrscheinlichkeit des Auftretens des Fehlers verringert oder die Wahrscheinlichkeit seiner Entdeckung erhöht wird. Auch hier gilt: Sind keine geeigneten Maßnahmen möglich, muss begründet und dokumentiert werden, warum die bestehenden ausreichen.
- Low = Niedrige Priorität für die Maßnahme: Wenn es Maßnahmen zur Reduzierung des Risikos gibt, können diese umgesetzt werden.
Letztlich sollten die einzelnen Faktoren getrennt betrachtet werden, um die Bedeutung eines Fehlers und mögliche Maßnahmen zur Fehlervermeidung oder Fehlerbeseitigung besser beurteilen zu können. Wie die drei Faktoren A, E und B zu bewerten sind, ergibt sich aus den Formblättern des VDA oder der DGQ.
Ziel dabei ist, die Fehler so zu bewerten, dass sichtbar wird, welche Fehler in jedem Fall vermieden werden müssen und welche Maßnahmen entsprechend wichtig sind und durchgeführt werden müssen. Damit sollen die Fehler vermieden oder die Folgen verringert werden.
Optimierung und Maßnahmenumsetzung
In diesem FMEA-Schritt werden Maßnahmen geplant, um die Fehlfunktionen, ihre Ursachen und ihre Folgen, soweit es geht, auszuschließen. Vor allem ist es wichtig, solche Fehler zu bearbeiten, die ein hohes Gefahrenpotenzial oder Sicherheitsrisiko haben.
Je nach betrachtetem System können damit Änderungen am System und an einzelnen Elementen verbunden sein, damit die Fehlerursache nicht mehr auftritt oder dass ihr Schaden geringer wird. Vorteilhaft sind außerdem Maßnahmen, die dazu führen, dass Fehler schnell, rechtzeitig und einfach erkannt werden.
Für die Planung und Umsetzung der Maßnahmen kann ein gesondertes Projekt definiert werden. Dort können andere oder weitere Personen eingebunden sein. Während der Umsetzung muss geprüft werden, ob die Ziele und Verbesserungen erreicht werden, die mit der Maßnahme verfolgt werden. Dazu kann es notwendig sein, dass die FMEA ein weiteres Mal durchgeführt wird.
Ergebnisse dokumentieren
Zum Abschluss des FMEA-Projekts hält die Projektleitung die Ergebnisse aus dem FMEA-Prozess fest und dokumentiert sie für das Unternehmen, für andere FMEA-Teams und für die Fachabteilungen: Entwicklung, Produktion, Produktmanagement etc. Dabei werden die möglichen Fehler, ihre Ursachen, spezifische Risiken und Maßnahmen zur Vermeidung benannt und erläutert.
Zur Strukturierung der FMEA-Dokumentation hilft folgende Systematik:
- FMEA-Projektteam: wer war dabei
- analysiertes Produkt oder Prozess
- Aufwand für das FMEA-Projekt
- die 10 größten Risiken
- Erläuterungen dazu auf der Grundlage von AP bzw. RPZ
- Benennung der Ursachen, die ein hohes Risiko haben
- empfohlene und umgesetzte Maßnahmen
- Einsparpotenzial
Wenn Sie die Ergebnisse der FMEA dokumentieren, gewinnt das Unternehmen eine protokollierte Wissensbasis, mit der laufende und künftige Entwicklungsprojekte besser unterstützt werden. Und wenn so regelmäßig FMEA-Projekte durchgeführt werden, kann sich eine entsprechende Qualitätskultur in Ihrem Unternehmen entwickeln.
Vorgehensmodell für FMEA festlegen
Orientieren Sie sich an dem Vorgehensmodell zur Durchführung einer FMEA, wie es in den für Ihre Branche geltenden Standards festgelegt ist. Zum Beispiel nach dem Standard des VDA und der AIAG, wie er oben beschrieben ist.
Klären Sie für Ihr Unternehmen, ob wichtige Kunden Vorgaben dazu machen, wie eine FMEA durchzuführen ist. Gibt es geltende Qualitätssicherungsvereinbarungen? Was ist dort zur FMEA geregelt?
Unabhängig davon, welches Vorgehensmodell für Ihr Unternehmen relevant ist und eingesetzt wird, können Sie sich an der oben genannten Schrittfolge zur Vorgehensweise orientieren. Die jeweiligen Informationen, Analysen und Bewertungen können Sie in der folgenden Vorlage zusammenstellen. Damit werden Sie in Einzelschritten durch die FMEA geführt.
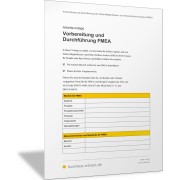
FMEA durchführen
Entwickeln Sie so die für Ihr Unternehmen praktikable und relevante Vorgehensweise bei FMEA-Projekten. Die folgenden Vorlagen sind Hilfsmittel für einzelne Schritte der FMEA, zur Diskussion im FMEA-Team und im Workshop sowie zur Visualisierung der Ergebnisse.
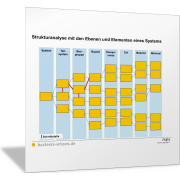
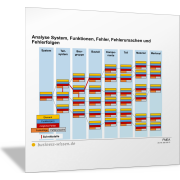
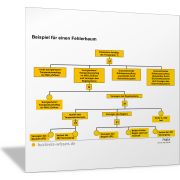
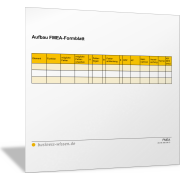
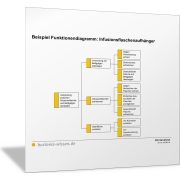
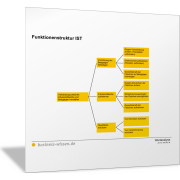
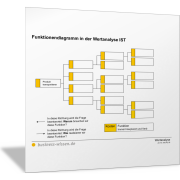
FMEA-Formblatt nutzen
Ein zentrales Werkzeug zur Zusammenstellung aller wichtigen Informationen zur FMEA ist das FMEA-Formblatt. Dazu finden Sie hier zwei Excel-Vorlagen.
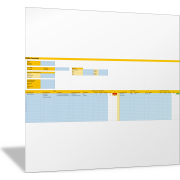
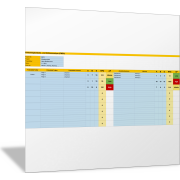
Zur Durchführung dieser Arbeitsschritte im FMEA-Projekt werden unterschiedliche Methoden und Werkzeuge eingesetzt. Eine Auswahl der wichtigen ist im folgenden Abschnitt des Handbuch-Kapitels erläutert.
„Fehler-Möglichkeiten- und Fehler-Einfluss-Analyse (FMEA)“ kaufen.