Wertstromanalyse (Value Stream Mapping)Das Wertstrom-Diagramm und seine Symbole als Basis der Wertstromanalyse
Mit der Wertstromanalyse Prozesse grafisch abbilden
Die Wertstromanalyse ist eine Form zur Visualisierung von Prozessen und Abläufen. Sie basiert auf unterschiedlichen Symbolen, die jeweils eine definierte Bedeutung haben. Und sie stellt ausgewählte Kennzahlen in einem Wertstrom-Diagramm oder auf einer Wertstrom-Karte dar.
Beispiel: Wertstrom-Diagramm zur Darstellung eines einfachen Prozesses
Abbildung 1 zeigt ein Beispiel eines Wertstrom-Diagramms für einen einfachen Prozess.
In diesem Bild werden unterschiedliche Kategorien von Informationen sichtbar:
- Prozess, Prozessschritte, Abläufe, Tätigkeiten, Aktivitäten
- Material, Teile, Zwischenprodukte, Endprodukte und ihre Logistik
- Informationen, Informationsfluss, Medien
- Zeitraster (Timeline)
- Bewertungen, Verbesserungspotenziale, Risiken
Für das Wertstrom-Diagramm in Abbildung 1 werden unterschiedliche Symbole und Bezeichnungen verwendet. Diese sind im Folgenden erklärt.
Prozess, Prozessschritte, Abläufe, Tätigkeiten, Aktivitäten im Wertstrom-Diagramm darstellen
Folgende Symbole werden eingesetzt, um den Prozess mit den einzelnen Prozessschritten, einzelnen Tätigkeiten oder Aktivitäten aufzuzeigen. Damit wird eine logische, technisch oder organisatorisch bedingte Reihenfolge der Prozessschritte sichtbar.
Jeder Prozess hat einen Anfang (Start) und ein Ende (Stopp). Diese ergeben sich aus dem Prozess, den Sie im Rahmen der Wertstromanalyse beschreiben und analysieren wollen. Damit der Prozess starten kann, braucht er einen Input – meistens in Form von Materialien. Diese werden von einem internen oder externen Lieferanten bezogen. Das Produkt oder Ergebnis des betrachteten Prozesses wird dann an einen internen oder externen Kunden übergeben, der es angefordert oder gekauft hat.
Die Symbole zur Darstellung der Prozessschritte, Tätigkeiten und Aktivitäten in einem Wertstrom-Diagramm sehen so aus:
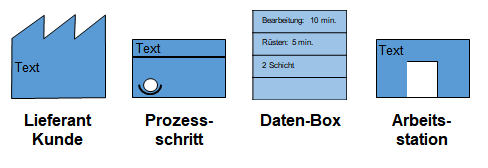
Lieferant; mit „Text“ zu geliefertem Material, Liefermengen, Lieferzeiten etc.
Kunde; mit „Text“ zu gelieferten Produkten und Erzeugnissen, Liefermengen, Lieferzeiten etc.
Prozess oder Prozessschritt und Aktivität mit Symbol für tätige Person(en) und „Text“ zur Bezeichnung des Prozessschritts; meistens verbunden mit einer Tätigkeit wie fertigen, montieren, prüfen, härten, verpacken, beraten etc.
Daten-Box mit Kennzahlen oder prozessspezifischen Merkmalen; die angegebenen Daten und Informationen sind Grundlage für die Analyse des Wertstroms; sie zeigen meist Ressourcen, Rahmenbedingungen, Zeitaufwand oder Kosten.
Arbeitsstation im Prozess, an der meist mehrere Tätigkeiten in technisch zwingender Folge oder automatisch durchgeführt werden; zum Beispiel ein Bearbeitungszentrum in der Fertigung oder eine automatisierte Montagelinie. Diese werden (zunächst) nicht im Detail analysiert.
Material, Teile, Zwischenprodukte, Endprodukte und Logistik im Wertstrom-Diagramm darstellen
Folgende Symbole werden genutzt, um den Materialfluss in einem Prozess-Diagramm abzubilden. Dieser Materialfluss wird meist nach dem sogenannten Kanban-System organisiert. Dementsprechend werden die Symbole für Kanban-Karten und Kanban-Lager eingesetzt.
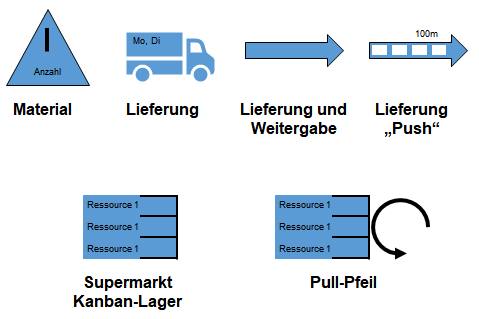
Material, Teile, Zwischenprodukte, Endprodukte, die im Laufe des Prozesses eingesetzt oder genutzt und bearbeitet, hergestellt oder montiert werden. Es werden nicht alle Teile einer Stückliste im Wertstrom-Diagramm aufgeführt, sondern nur Teile, die im Prozessschritt das Objekt der Wertschöpfung sind, besondere Bearbeitung erfordern, wichtig für die Qualität sind, lange Beschaffungszeiten haben oder ein Engpass sein können.
Lieferung von Teilen vom Lieferanten zum Prozessstart oder von Endprodukten nach Prozessende zum Kunden.
Lieferungen und Weitergabe von Teilen oder Zwischenprodukten innerhalb des Prozesses (Materialfluss); diese Pfeile sind Verbinder zwischen einzelnen Prozessschritten.
Lieferungen und Weitergabe in Form von „Push“; die in einem Prozessschritt hergestellten Teile oder Zwischenprodukte werden in den nächsten Prozessschritt „gedrückt“, sobald sie hergestellt sind.
Supermarkt oder Kanban-Lager, in dem Material, Teile oder Zwischenprodukte nach dem Kanban-Prinzip (zwischen-) gelagert und abgerufen werden. Beim Erreichen eines Meldebestands wird eine Kanban-Karte an den vorgelagerten Prozess gegeben.
Material, Teile oder Zwischenprodukte werden aus dem Supermarkt entnommen; „Pull-Pfeil“.
Informationen, Informationsfluss, Medien
Folgende Symbole werden genutzt, um den Informationsfluss sowie Planungsaktivitäten in einem Prozess-Diagramm abzubilden.
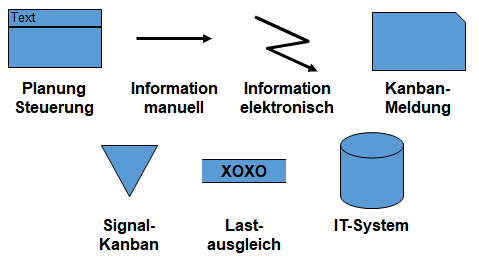
Aktivitäten zur Planung und Steuerung von Prozessen werden im Wertstrom-Diagramm aufgeführt, wenn diese Prozesse anstoßen, Ziele vorgeben oder Rahmenbedingungen setzen.
Wenn Informationen von einer Stelle an eine andere weitergegeben werden, wird dies in Form eines Informationspfeils dargestellt. Der gerade Informationspfeil symbolisiert die manuelle Informationsweitergabe (persönlich oder auf Papier). Der gezackte Informationspfeil die elektronische Informationsweitergabe; zum Beispiel EDI, LAN, WAN, Intranet, Internet etc.
Die Kanban-Meldung (Karte) signalisiert dem vorgelagerten Prozess oder Prozessschritt, dass Material benötigt wird. Dabei wird vermerkt, wie viel Material benötigt wird (Bestellmenge oder Losgröße) und welche Lieferzeit erwartet wird.
Das Symbol Signal-Kanban zeigt an, dass an dieser Stelle im Prozess der Bestand auf ein Minimum reduziert wird. Der Bestand an Material wird visuell überwacht. Sobald ein Bestandsminimum erreicht ist, wird das Material nachproduziert.
In einem Prozessschritt werden die angeforderten Produktmengen in Lose aufgeteilt, damit die Prozesslast ausgeglichen ist; das Symbol markiert diesen Lastausgleich. Damit sollen hohe Bestände und lange Wartezeiten bei nachgelagerten Prozessschritten vermieden werden.
Für die Planung und Steuerung eines Prozesses werden oft IT-Systeme eingesetzt, die Daten verarbeiten und Informationen zur Verfügung stellen. Das Symbol für IT-Systeme steht beispielsweise für ERP- oder MRP-Systeme, wie sie für die Produktionsplanung, Ressourcenplanung und die Steuerung von Material und Arbeitsstationen eingesetzt werden.
Zeitraster oder Timeline
Eine wichtige Funktion der Wertstromanalyse ist es aufzuzeigen, wie lange ein Prozess dauert, welche Durchlaufzeit er hat. Damit ist die Zeit in Minuten, Stunden oder Tagen gemeint, die es braucht vom Prozessstart bis zur Lieferung des Prozessergebnisses an den Kunden (Prozessende). Dabei muss genau definiert sein, was den Prozessstart auslöst; zum Beispiel der eingehende Auftrag eines Kunden.
Die Timeline im Wertstrom-Diagramm wird in der folgenden Weise dargestellt:
Mit dem Symbol der Timeline soll deutlich werden, was die Gesamtzeit des Prozesses aus Sicht des Kunden, also die Durchlaufzeit maßgeblich beeinflusst. Dazu wird für einen einzelnen Prozessschritt dargestellt:
- Bearbeitungszeit: wie lange die eigentliche Leistungserstellung selbst dauert (hängt ab vom Umfang des Auftrags und der durchschnittlichen Bearbeitungszeit pro Stück)
- Wartezeit oder Liegezeit: wie lange das bearbeitete Material vor und nach der Bearbeitung ohne wertschöpfende Aktivitäten wartet
Nur die eigentliche Bearbeitungszeit ist wertschöpfend. Mit der Darstellung der Timeline wird also sichtbar, wenn Teile sehr lange, nicht wertschöpfend warten oder liegen.
Am Ende einer Timeline wird mit einem Symbol (Rechteck) angezeigt, wie lange die Durchlaufzeit und wie lange die eigentliche Bearbeitungszeit (wertschöpfend) für den jeweiligen Prozess ist.
Sie sollten bei der Darstellung der Timeline erläutern, was genau Sie mit der Bearbeitungszeit meinen und was damit gemessen wird. Das gilt auch für die Wartezeit oder Liegezeit. Bei einer genauen Prozessanalyse lassen sich Ausführungszeit, Rüstzeiten, Überführungszeiten, Liegezeiten, Pausenzeit oder Wartungszeiten unterscheiden. Um Missverständnisse zu vermeiden, sollten Sie definieren, welche Zeiten Sie für Ihre Wertstromanalyse betrachten und in der Timeline darstellen.
Bewertungen, Verbesserungspotenziale, Risiken
Für die Analyse und Bewertung des Prozesses, die eigentliche Wertstromanalyse, werden mögliche Schwachstellen oder Risiken des Prozesses im Wertstrom-Diagramm sichtbar gemacht. Dazu werden die Stellen mit dem folgenden Symbol markiert, die als problematisch eingeschätzt oder erkannt wurden.
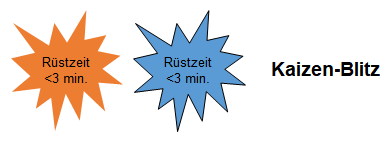
Mit dem Kaizen-Blitz werden diese kritischen Elemente im Prozess markiert und benannt, was verbessert oder verändert werden sollte.
Software für die Prozessvisualisierung
Einfache Wertstromanalyse-Diagramme können mit der weit verbreiteten Standard-Software PowerPoint (Microsoft Office) erstellt werden. Aufwendiger, aber flexibler ist die Software Visio (Microsoft); für diese gibt es Add-ins mit den Symbolen für die Wertstromanalyse. Alternative Produkte speziell für die Wertstromanalyse sind Lucidchart oder EDraw.
Prozesse mit den Symbolen der Wertstromanalyse visualisieren
Nutzen Sie die standardisierten Symbole und Element für die Darstellung Ihrer Prozesse und Abläufe in der Form eines Wertstrom-Diagramms. In der folgenden Vorlage finden Sie die Symbole als PowerPoint-Elemente, die Sie in Ihre Vorlage kopieren können.
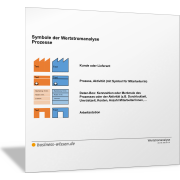
In der folgenden PowerPoint-Vorlage sind die Symbole aufbereitet, die bei der Wertstromanalyse und beim Erstellen eines Wertstrom-Diagramms genutzt werden. Jedes Symbol ist auf einer DIN-A4-Seite dargestellt. Sie können die Seiten jeweils so oft drucken, wie sie benötigt werden.
Dann nutzen Sie diese Ausdrucke, um gemeinsam mit dem Team einen Prozess an der Wand (mit braunem Packpapier) zu visualisieren und zu analysieren. Sie beschreiben die Vorlagen mit den entsprechenden Informationen und kleben diese an die Wand. So entsteht ein nachvollziehbares Bild zu Ihrem Prozess.
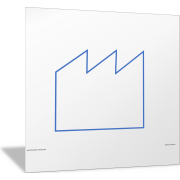
Beispiel für ein Wertstrom-Diagramm
In der folgenden Abbildung und PowerPoint-Vorlage sehen Sie ein Beispiel dafür, wie ein Prozess als Wertstrom-Diagramm dargestellt werden kann.
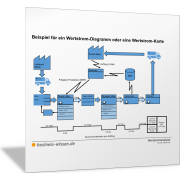
Prozesse analysieren, Schwachstellen und Verbesserungspotenziale erkennen
Analysieren und bewerten Sie dann Ihre Prozesse oder einzelne Prozessschritte und Prozessaktivitäten im Hinblick auf:
- lange Wartezeiten
- hohe Bestände
- unnötige Prozessschritte
- falsche Planvorgaben
- Probleme mit der Prozess- oder Produktqualität
- Probleme bei Lieferung
- fehlende Informationen oder Daten
Zahlreiche Vorlagen, Analyseinstrumente und Erläuterungen für eine detaillierte Prozessanalyse finden Sie in den Handbuch-Kapiteln: Prozessmanagement, SIPOC und Kaizen.