KanbanWie man Parameter der Kanban-Steuerung berechnet
Die Parameter für die Kanban-Steuerung
Für die Kanban-Steuerung müssen einige Parameter ermittelt und berechnet werden. Sie brauchen diese, um das System auszubalancieren und einen möglichst geringen Lagerbestand zu haben – ohne dass der Produktionsfluss ins Stocken gerät. Folgende Parameter sind für Kanban wichtig.
Verbrauchsgeschwindigkeit
Die Verbrauchsgeschwindigkeit gibt an, wie viele Teile pro Tag, pro Woche oder pro Monat verbraucht werden. Diese Menge lässt sich nicht exakt angeben, da sie aus unterschiedlichen Gründen schwanken kann. Im Supermarkt weiß niemand genau, wie viele Pralinenschachteln pro Woche verkauft werden. Deshalb braucht es statistische Methoden, um den wahrscheinlichen Verbrauch zu berechnen.
Wenn dann mal weniger verbraucht wird, wird nach den Kanban-Regeln einfach später bestellt. Denn das Kanban-Signal erscheint entsprechend später. Wenn mehr verbraucht wird, erscheint das Kanban-Signal entsprechend früher.
Kritisch wird es nur, wenn in der Zeit zwischen dem Erscheinen des Kanban-Signals und dem Wiederbefüllen des Lagers plötzlich so viel verbraucht wird, dass das Lager leer ist, bevor es wieder befüllt wird.
Kanban-Meldebestand mit Puffer
Deshalb muss der Kanban-Meldebestand einen Puffer haben. Er muss so berechnet werden, dass auch höhere Bedarfe erfüllt werden können und (ausnahmsweise etwas) längere Beschaffungszeiten kein Problem sind. Bis dieser Kanban-Meldebestand mit Puffer festgelegt wird, dauert es einige Zeit, in der Verbräuche und Lieferzeiten gemessen und statistisch ausgewertet werden, um Erfahrungswerte (Wahrscheinlichkeiten) zu ermitteln.
In der Praxis wird der Kanban-Meldebestand regelmäßig geprüft und bei Bedarf angepasst. Zudem wird dafür gesorgt, dass die Lieferung in möglichst kurzer Zeit erfolgt, indem die vorgelagerten Prozesse verbessert und Produktionszeiten reduziert werden. Ziel ist: Kanban-Meldebestand und Puffer ständig zu verringern.
Kanban-Steuerung auf Behälter-Ebene
Wenn die Kanban-Steuerung auf Behälter-Ebene erfolgt, dann ist ein Behälter gerade so groß, dass er den Kanban-Meldebestand mit Puffer enthält. Sobald ein Behälter aus dem Kanban-Lager entnommen wird, werden die daran befestigte Kanban-Karte und der leere Behälter an die vorgelagerte Produktionsstufe gesendet mit dem Hinweis: Diesen Behälter wieder befüllen.
Wiederbeschaffungszeit
Wie der Kanban-Meldebestand und der Puffer berechnet werden, hängt unter anderem von der Wiederbeschaffungszeit ab.
Wie lange dauert es, bis nach dem Erscheinen des Kanban-Signals das Lager wieder auf den gewünschten Bestand aufgefüllt ist?
Diese Wiederbeschaffungszeit ergibt sich aus der Zeit, die benötigt wird für:
- Bestellung
- Produktion
- Lieferung oder Transport
- Qualitätsprüfung bei Wareneingang (sofern notwendig)
Diese Zeiten sollten so gering wie möglich sein. Dazu werden die entsprechenden Prozesse immer wieder überprüft und nach Möglichkeiten zur Zeiteinsparung gesucht; zum Beispiel durch Automatisierung bei der Bestellung, durch kürzere Rüst- und Bearbeitungszeiten in der Produktion oder durch Wegfall der Qualitätsprüfung aufgrund von vorbeugender Qualitätssicherung in der Produktion. Solche Maßnahmen werden im Toyota-Produktionssystem und bei Lean Management mit dem Begriff Heijunka zusammengefasst.
Bestell- und Produktionsmenge
Mit der Bestellung von Teilen zum Wiederbefüllen des Lagers muss festgelegt werden, wie viele Teile jeweils bestellt werden. Maximal sind das so viele, wie ins Lager passen. Gleichzeitig will man die Bestellmenge möglichst gering halten, um Kapitalkosten zu sparen; Teile auf Lager sind gebundenes Kapital. Und die vorgelagerte Produktion soll nicht mit einem Großauftrag über längere Zeit ausgelastet sein.
Andererseits: Häufige Bestellungen führen zu höherem Bestellaufwand. Deshalb muss das Optimum gefunden werden. In einem ersten Ansatz eignet sich dafür die Andler-Formel, mit der sich die Beschaffungsmenge berechnen lässt. Sie ist abhängig von:
- Jahresbedarfsmenge für diesen Artikel in Stück (oder einer entsprechenden Mengeneinheit)
- fixe Produktionskosten pro Los oder Bestellkosten pro Bestellvorgang in Euro
- Stückkosten oder Einkaufspreis je Mengeneinheit in Euro
- Zinssatz und Lagerkostensatz in Prozent
Wenn der Artikel im eigenen Unternehmen hergestellt wird, geht es um die Abwägung von Lagerkosten und Rüstkosten in der vorgelagerten Produktion. Dazu wird mit der Andler-Formel die optimale Bestellmenge beziehungsweise die mit einem Auftrag produzierte Menge, die Losgröße, berechnet.
Visualisierung des Kanban-Bestands im Lager
Mit diesen Parametern lässt sich der Kanban-Prozess wie in Abbildung 2 visualisieren.
Die Abbildung zeigt einige Merkmale der Bestandsführung nach der Kanban-Methode:
- Die Verbrauchsgeschwindigkeit (a/b) variiert; in den einzelnen Verbrauchsphasen wird mal mehr, mal weniger verbraucht.
- Die Wiederbeschaffungszeit (d) kann variieren, sollte aber möglichst gering und verlässlich sein (keine großen Variationen).
- Die Bestell- oder Produktionsmenge (f) ist immer die gleiche; sie darf aber nicht größer sein als die maximale Lagerkapazität abzüglich des Kanban-Meldebestands.
- In Verbrauchsphase 3 ist die Verbrauchsgeschwindigkeit sehr groß. Während der Wiederbeschaffungszeit reicht der Puffer gerade aus; beim Lagerbestand von (fast) 0 wird wieder befüllt.
Aus diesem beispielhaften Verlauf des Lagerbestands wird deutlich, dass die durchschnittlichen Verbrauchsgeschwindigkeiten und Wiederbeschaffungszeiten, sowie deren jeweiliges Minimum und Maximum, maßgeblich dafür sind, wie die anderen Parameter festgelegt werden. Sprich: maximaler Lagerbestand (Größe des Lagers), Puffer, Kanban-Meldebestand und Bestell- oder Produktionsmenge.
Wie werden die Parameter für die Kanban-Steuerung berechnet?
Mit den folgenden Formeln berechnen Sie die einzelnen Parameter für die Kanban-Steuerung. Daraus leiten Sie ab, wie Sie die Produktionsprozesse einrichten und welche Lagerkapazitäten Sie schaffen sollten in dem Bereich, in dem Sie die Kanban-Methode einsetzen wollen.
Minimaler Kanban-Meldebestand =
durchschnittliche Verbrauchsgeschwindigkeit (Stück pro Tag) x Wiederbeschaffungszeit (Tage)
Dabei ist zu beachten:
- Die durchschnittliche Verbrauchsgeschwindigkeit schwankt, da der Bedarf nicht sicher vorhergesagt werden kann. Deshalb wird mit Durchschnittswerten oder Erfahrungswerten gerechnet.
- Die Wiederbeschaffungszeit ist der Zeitraum, der vergeht vom Erscheinen des Kanban-Signals (Lager fast leer) bis zum Wiederbefüllen des Lagers (Lager wieder voll).
- Die Einheiten für die durchschnittliche Verbrauchsgeschwindigkeit und die Wiederbeschaffungszeit hängt ab von der Art des Artikels: Stückgut (Anzahl), Schüttgut (Gewicht), Charge (Volumen); sowie von der üblichen Planungszeit: Tag, Woche etc.
Tatsächlicher Kanban-Meldebestand = Bestand bei Auslösen des Kanban-Signals =
minimaler Kanban-Meldebestand + Pufferbestand
Dabei ist zu beachten:
- Der Puffer kann zum Beispiel daraus berechnet werden, welche maximale Verbrauchsgeschwindigkeit im Laufe eines Jahres aufgetreten ist, sodass auch solche hohen Bedarfe aus dem Kanban-Lager bedient werden können.
- Außerdem kann es zu Lieferverzug kommen, wenn die vorgelagerte Produktion Störungen oder Qualitätsprobleme hat.
- Meist wird deshalb ein Prozentanteil des minimalen Kanban-Meldebestands als Puffer herangezogen.
durchschnittliche Verbrauchsgeschwindigkeit in Stück pro Tag =
Summe der aus dem Lager in vier Wochen entnommenen Teile in Stück / 28 Tage
Dabei ist zu beachten:
- Es hängt von der Art der Teile ab, über welchen Zeitraum die durchschnittliche Verbrauchsgeschwindigkeit berechnet wird; statt 28 Tage sind auch 7 Tage oder 365 Tage möglich.
- Saisonale Effekte können eine Rolle spielen und sollten beachtet werden.
- Außerdem können Trends eine Rolle spielen; wenn die Gesamtnachfrage steigt, steigt auch die Verbrauchsgeschwindigkeit.
- Ausreißer oder Extremwerte sollten hinterfragt werden.
Wiederbeschaffungszeit in Tagen =
Bestellzeit + Wartezeit bis Auftragsbeginn in der vorgelagerten Produktionsstufe + Rüstzeit + (Bearbeitungszeit pro Stück x Bestellmenge) + Lagerzeit nach der Produktion + Transportzeit ins Kanban-Lager
Dabei ist zu beachten:
- Wie lange diese einzelnen Prozesszeiten sind, muss über einen geeigneten Zeitraum gemessen werden.
- Ziel muss sein, dass die Wiederbeschaffungszeit möglichst kurz ist und nicht schwankt.
Bestellmenge = Produktionsmenge =
maximaler Lagerbestand – tatsächlicher Kanban-Meldebestand
Dabei ist zu beachten:
- In der Zeit der Wiederbeschaffung werden vermutlich weitere Teile aus dem Lager entnommen; das bedeutet, dass der maximale Lagerbestand nicht immer wieder erreicht wird.
- Nur wenn in der Wiederbeschaffungszeit nichts entnommen wird, wird das Lager bis zur maximalen Kapazität gefüllt.
maximaler Lagerbestand = Lagerkapazität
Eine der wichtigsten Fragen bei der Einführung und Optimierung der Kanban-Methode ist: Wie hoch ist der maximale Lagerbestand für den jeweiligen Artikel? Eine eindeutige Antwort darauf gibt es nicht. Ziel ist, diesen maximalen Lagerbestand möglichst niedrig festzulegen, denn:
- Hohe Lagerbestände bedeuten gebundenes Kapital und damit hohe Kapitalkosten.
- Lagerbestände können verderben oder technisch veralten.
- Hoher Lagerbestand braucht viel Platz, das Lager muss entsprechend dimensioniert werden.
Andererseits führt ein niedriger maximaler Lagerbestand dazu, dass der Kanban-Meldebestand schon nach kurzer Zeit wieder erreicht wird. Es muss wieder bestellt werden, was diese Folgen haben kann:
- Jede Bestellung bedeutet einen Aufwand oder Kosten in Abhängigkeit von der Art des Bestellprozesses.
- Die vorgelagerte Produktion stellt nur geringe Stückzahlen in einem Produktionsauftrag her (kleine Losgröße); das kann zu hohen Rüstkosten und mehr Planungsaufwand führen.
Es muss also abgewogen und optimiert werden. Im ersten Ansatz hilft oft die Andler-Formel:
Bestellmenge = Produktionsmenge =
Wurzel aus ((200 x Jahresbedarf x Fixkosten pro Bestellung) / (variable Bestellkosten x Lagerkostensatz in Prozent))
Letztlich soll die Bestellmenge aber geringer sein und häufiger bestellt werden, indem die Fixkosten pro Bestellung reduziert oder eliminiert werden; zum Beispiel durch minimale Rüstzeiten.
Anzahl Kanban =
Tatsächlicher Kanban-Meldebestand / Behälterinhalt in Stück
Dabei ist zu beachten:
- Die Anzahl der Kanban wird berechnet, wenn die Kanban-Steuerung auf der Ebene der Behälter erfolgt.
- Für jeden Artikel wird der Behälterinhalt in Abhängigkeit von der durchschnittlichen Verbrauchsrate gewählt.
- Die Anzahl der Kanban gibt die Zahl der Behälter an, die für den Artikel im Umlauf sind.
Parameter für die Kanban-Steuerung berechnen
Bestimmen Sie dann die einzelnen Kanban-Parameter, wie sie oben beschrieben und als Formel definiert sind für die Teile, die Sie entsprechend steuern wollen. Nutzen Sie dafür die folgende Excel-Vorlage.
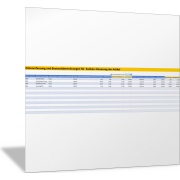
Darin sind die entsprechenden Formeln hinterlegt. Sie können beliebig viele Teile (Artikel) eingeben und erfassen jeweils:
- Artikel-Nummer und Bezeichnung sowie die Bezeichnung für eine Mengeneinheit
- Durchschnittsverbrauch
- Durchschnitt für die Wiederbeschaffungszeit
- Pufferbestand
- fixe Gesamtkosten bei einer Bestellung oder einem Produktionsauftrag
- variable Kosten pro Mengeneinheit bei Bestellung oder Produktion
- Lagerkostensatz (in Prozent)
Berechnet werden dann:
- Kanban-Meldebestand
- Jahresbedarf
- Bestellmenge
- notwendige Lagerkapazität
Optimale Bestellmenge oder Losgröße für die Produktion berechnen
Mit der folgenden Excel-Vorlage berechnen Sie mithilfe der Andler-Formel die optimale Bestellmenge oder Losgröße für ein einzelnes Kanban-Teil.
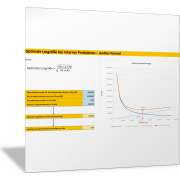
Pufferbestand für das Kanban-Lager berechnen
Wenn Sie sicherstellen wollen, dass das Lager jederzeit lieferfähig ist, müssen Sie den Pufferbestand entsprechend berechnen. In der folgenden Excel-Vorlage ist eine entsprechende Formel hinterlegt, mit der Sie den Sicherheitsbestand bei einem 100-Prozent-Servicegrad berechnen.
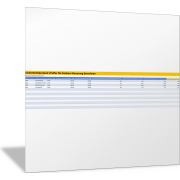
In dieser Vorlage berechnen Sie den Pufferbestand für beliebig viele Teile (Artikel). Dazu erfassen Sie:
- Durchschnittsverbrauch pro Tag
- maximaler Verbrauch an einem Tag
- maximale Mengenabweichung durch zu geringe Lieferung bei Nachbestellung (Unterlieferung) in Mengeneinheiten
- maximale Abweichung von der geplanten Wiederbeschaffungszeit; Terminverzögerung bei der Lieferung in Tagen
- durchschnittliche Wiederbeschaffungszeit in Tagen
Mit der folgenden Excel-Vorlage berechnen Sie die Parameter der Kanban-Steuerung für einen ausgewählten Artikel. Dabei erfassen Sie zunächst für einen beliebigen Zeitraum oder fortlaufend (pro Tag) die notwendigen Daten für die Berechnung. Aus den ermittelten Daten wird dann jeweils ein Durchschnitt berechnet. Daraus werden berechnet:
- Kanban-Meldebestand
- Bestellmenge (nach Andler)
- notwendige Lagerkapazität
- täglicher Lagerbestand
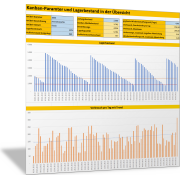
In der Vorlage wird farblich angezeigt, wenn der Lagerbestand den Kanban-Meldebestand erreicht wird (hellrot) und wenn der Pufferbestand erreicht wird (dunkelrot). Mit der Vorlage erfassen Sie auch die Lieferungen, die das Lager wieder befüllen und die farbliche Markierung aufheben.