Maschinenfähigkeit und Prozessfähigkeit berechnenWie Sie die Maschinenlaufzeit steigern
- Was ist die Maschinenlaufzeit?
- Wie wirkt sich die Maschinenlaufzeit aus?
- Wartungsstrategie optimieren: Predictive Maintenance
- Produktionsprozesse anpassen
- Rüstprozesse vereinfachen
- Automatisierung und Digitalisierung
- Produktionsplanung optimieren
- Prozesskontinuität verbessern
- Retrofit-Maßnahmen ergreifen
- 4 Vorlagen im Praxisteil
Was ist die Maschinenlaufzeit?
Die Maschinenlaufzeit bezeichnet in der Produktion und Fertigung die Zeit, während der eine Maschine tatsächlich in Betrieb ist und arbeitet, also Materialien bearbeitet oder Produkte herstellt. Sie steht im Gegensatz zur Stillstandszeit, in der die Maschine aus verschiedenen Gründen (zum Beispiel: Wartung, Rüstvorgänge, Fehlfunktionen) nicht aktiv ist.
Bei der Maschinenlaufzeit handelt es sich um eine wichtige Kennzahl zur Bewertung der Wirtschaftlichkeit einer Fertigungseinrichtung, da sie unmittelbar mit der Produktivität einer Anlage zusammenhängt. Eine hohe Maschinenlaufzeit bedeutet in der Regel, dass die Produktion reibungslos verläuft und die Maschinen optimal ausgelastet ist.
Die Maschinenlaufzeit wird durch folgende Faktoren beeinflusst:
- Rüstzeiten
- Wartung
- Materialverfügbarkeit
- Mitarbeiterverfügbarkeit
- technische Störungen
- Produktionsprozesse
- Planungsprozesse
In der Fertigungssteuerung wird oft die Gesamteffektivität der Anlage (OEE) als Maß für die Maschinenlaufzeit herangezogen, die auch Qualität und Leistung der Produktion mitberücksichtigt.
Die folgende Abbildung zeigt, durch welche Maßnahmen die Maschinenlaufzeit und damit die Rentabilität der Maschine gesteigert werden kann. Manche Maßnahmen sind einfach umzusetzen, andere setzen weitreichende Veränderungen voraus. Die Abbildung soll sichtbar machen, dass die Maßnahmen aufeinander aufbauen und kombiniert werden können.
Ziel ist es, unter den gegebenen Rahmenbedingungen eine maximale Maschinenlaufzeit zu erreichen, die auch durch weitere Maßnahmen nicht zu verbessern ist, ohne dass die Gesamtrentabilität des Maschineneinsatzes wieder sinkt (etwa durch Maßnahmen, die mehr kosten, als an zusätzlichem Gewinn durch höhere Maschinenlaufzeit erzielt wird).
Wie wirkt sich die Maschinenlaufzeit aus?
Die maximal möglichen Betriebsstunden in einem Jahr betragen 8.760 Stunden – so lange könnte eine Maschine theoretisch produktiv genutzt werden, wenn sie rund um die Uhr läuft. Doch in den meisten Unternehmen stehen die Maschinen so häufig oder lange an einem Stück still, dass die Maschinen nur zwischen rund 2000 und 4000 Stunden produktiv arbeiten.
Der wichtigste Grund dafür ist, dass im Unternehmen an Wochenenden, Feiertagen oder nachts nicht gearbeitet wird. Diese „bekannten und gewollten Ausfallzeiten“ gehen bei der Berechnung der Maschinenlaufzeit und der Rentabilität deshalb oft nicht mit ein.
So ergeben sich bei einer möglichen Laufzeit einer Maschine an 5 Tagen pro Woche, mit Betriebsferien von 4 Wochen pro Jahr und einem Zweischichtsystem mit 14 Arbeitsstunden pro Tag eine maximale Maschinenlaufzeit von 3.360 Stunden pro Jahr.
In dieser Zeit kann die Maschine aber auch nicht durchgängig arbeiten, weil sie immer wieder zuerst umgerüstet, gewartet, repariert oder programmiert werden muss. Fehlen den bedienenden Mitarbeitenden Informationen oder Werkzeuge oder müssen sie auf Arbeitsergebnisse anderer Kollegen oder Maschinen warten, steht die Maschine ebenfalls still.
Hier setzen die Maßnahmen zur Steigerung der Maschinenlaufzeit an.
Wie beeinflusst die Maschinenlaufzeit den Maschinenstundensatz?
Die Maschinenlaufzeit wirkt sich direkt auf den Maschinenstundensatz aus, der die Kosten pro Betriebsstunde einer Maschine wiedergibt. Je länger die Maschine läuft, desto mehr können die Fixkosten auf die Betriebsstunden verteilt werden, was den effektiven Stundensatz senkt.
Mit der folgenden Vorlage berechnen Sie den Maschinenstundensatz für Ihre Maschinen.
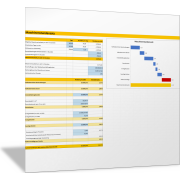
Wartungsstrategie optimieren: Predictive Maintenance
Die Wartungsstrategie hat einen entscheidenden Einfluss auf die Wirtschaftlichkeit und Lebensdauer von Maschinen. Predictive Maintenance (vorausschauende Wartung) ist dabei eine der fortschrittlichen Methoden, da sie auf Echtzeitdaten und Vorhersagemodellen basiert, um Ausfälle, ungeplante Stillstände und eine nicht optimale Produktionsauslastung zu verhindern.
Die Predicitive Maintenance kombiniert zwei Ansätze:
- zustandsbasierte Wartung: Durch den Einsatz von Sensoren und Überwachungssoftware überwachen Sie den Zustand der Maschine in Echtzeit. Dadurch können Wartungsarbeiten vor einem Ausfall geplant und ungeplante Stillstände verhindert werden.
- vorbeugende Wartung: Durch regelmäßige Inspektionen und vorbeugende Wartungsarbeiten erkennen Sie potenzielle Probleme frühzeitig und vermeiden lange und teure Ausfallzeiten.
Zustandsbasierte Wartung
Der Zustand einer Maschine wird kontinuierlich überwacht, um Wartungsmaßnahmen nur dann durchzuführen, wenn der Bedarf besteht. Dafür werden Sensoren und Überwachungssoftware eingesetzt, die wichtige Parameter wie Temperatur, Vibration, Ölstand, Druck oder Geräuschpegel erfassen.
Die Daten, die von den Sensoren gesammelt werden, geben Aufschluss über den Maschinenzustand. Wenn bestimmte Grenzwerte überschritten werden, signalisiert das ein potenzielles Problem.
Der Vorteil bei diesem Vorgehen: Wartungsarbeiten können geplant werden, bevor es zu Ausfällen kommt, was ungeplante Stillstände vermeidet. Dies ist besonders nützlich für kritische Anlagen, die kontinuierlich laufen müssen.
Beispiel:
Ein Sensor stellt eine erhöhte Vibration in einem Lager fest, was auf Abnutzung hindeutet. Das Wartungsteam ersetzt daraufhin sofort das Lager, bevor es zu einem Totalausfall kommt.
Vorbeugende Wartung (Preventive Maintenance)
Vorbeugende Wartung basiert auf der regelmäßigen Wartung von Maschinen, unabhängig davon, ob ein akuter Bedarf besteht. Dieser Ansatz zielt darauf ab, Ausfälle durch geplante Wartungstermine und Inspektionen zu verhindern.
Wartungspläne werden auf Basis von Betriebsstunden, Zyklen oder bestimmten Zeitintervallen festgelegt. Inspektionen und Austausche von Verschleißteilen erfolgen, bevor es zu einem erwarteten Versagen kommt. Die Wahrscheinlichkeit von teuren Maschinenausfällen und Produktionsstillständen wird reduziert.
Beispiel:
Ein Unternehmen beschließt, eine Maschine alle 500 Betriebsstunden zu inspizieren und bestimmte Teile regelmäßig zu ersetzen, unabhängig davon, ob sie sichtbare Abnutzungserscheinungen zeigen.
Produktionsprozesse anpassen
Identifizieren Sie Engpässe im Produktionsprozess, die zu längeren Maschinenstillständen führen, und entwickeln Sie Lösungen zur Beseitigung dieser Engpässe. Eine Vorlage zur Ermittlung von Engpässen finden Sie unten im Praxisteil.
Rüstprozesse vereinfachen
Durch die Implementierung von Methoden wie SMED (Single Minute Exchange of Die, Werkzeugwechsel im einstelligen Minutenbereich) können Rüstzeiten weiter reduziert und die Maschinenlaufzeit erhöht werden.
Bei der Reduzierung der Rüstzeit helfen außerdem die folgenden Maßnahmen:
- Parallelisierung von Rüstprozessen: Beispielsweise kann das nächste Werkzeug vorbereitet werden, während die Maschine noch läuft.
- Automatisierung des Rüstvorgangs: Automatisierte Systeme, wie Werkzeugwechsler oder automatische Justierungseinrichtungen, können den Rüstprozess stark verkürzen. Roboter werden eingesetzt, um Werkzeuge oder Material automatisch zu wechseln.
- Rüstprozesse in interne und externe Tätigkeiten unterteilen: Rüstvorgänge werden aufgeteilt in interne (während die Maschine stillsteht) und externe (während die Maschine läuft) Aktivitäten. Externe Tätigkeiten können vorbereitet werden, ohne dass die Maschine stillsteht.
- Optimierung der Arbeitsplätze und Werkzeuge: Ergonomische und übersichtlich organisierte Arbeitsplätze helfen, dass Werkzeuge schneller gefunden und genutzt werden. Das Platzieren von benötigten Werkzeugen und Materialien in direkter Nähe der Maschinen verkürzt unnötige Lauf- und Suchzeiten.
- Einsatz von Simulationen und digitaler Zwillinge: Durch die Verwendung von Simulationstechnologien und digitalen Zwillingen (digitale Repliken von Maschinen und Prozessen) können Rüstvorgänge im Vorfeld virtuell optimiert werden, um den realen Prozess zu verbessern.
- Planungsprozesse verbessern: Durch eine geschickte Auftrags- und Belegungsplanung können Rüstprozesse verkürzt werden. Ein Farbwechsel von einer hellen zu einer dunklen Farbe bedeutet meist geringere Reinigungszeit als von dunkel nach hell.
Automatisierung und Digitalisierung
Durch die Kombination von Automatisierung und digitalen Technologien wie IoT (Internet of Things) und Edge-Computing werden Maschinenprozesse in Echtzeit überwacht und automatisch angepasst. Automatisierte Systeme nehmen basierend auf den erfassten Daten sofortige Anpassungen vor, um:
- die Leistung zu maximieren,
- Engpässe zu vermeiden und
- die Maschinen kontinuierlich in optimalem Betrieb zu halten.
Dies reduziert manuelle Eingriffe und minimiert ungeplante Ausfallzeiten, wodurch die Maschinenlaufzeit steigt.
Durch den Einsatz von künstlicher Intelligenz und maschinellem Lernen können automatisierte Systeme kontinuierlich aus den Betriebsdaten lernen und eigenständig Optimierungen vornehmen. Diese selbstoptimierenden Systeme können Maschineneinstellungen dynamisch anpassen, um
- die Maschinenbelastung und daraus resultierende Defekte reduzieren,
- Lastspitzen zu managen und
- Zykluszeiten und Bearbeitungszeiten automatisch anzupassen.
Zusätzlich können sie frühzeitig Anomalien erkennen, die auf mögliche Ineffizienzen oder Störungen hindeuten, und automatisch Gegenmaßnahmen ergreifen, um eine möglichst lange und störungsfreie Laufzeit sicherzustellen.
Produktionsplanung optimieren
Stellen Sie sicher, dass die Produktionskapazitäten optimal genutzt werden. Dies kann durch eine bessere Abstimmung zwischen Auftragseingang und Produktionsplanung erfolgen.
Außerdem ist es wichtig, dass Ihre Maschinen flexibel eingestellt oder angepasst und dadurch genutzt werden können. Maschinen, die für verschiedene Produkttypen schnell umgerüstet werden können, ermöglichen eine höhere Auslastung und somit eine bessere Laufzeiteffizienz.
Prozesskontinuität verbessern
Stellen Sie sicher, dass die Materialversorgung kontinuierlich gewährleistet ist, um Unterbrechungen im Produktionsfluss zu minimieren. Eine Möglichkeit ist der Einsatz automatisierter Fördersysteme oder Roboter, um den Materialnachschub kontinuierlich und bedarfsgerecht zu gewährleisten. So werden Versorgungsengpässe vermieden.
Implementieren Sie ein visuelles Pull-System wie Kanban, um sicherzustellen, dass das benötigte Material immer verfügbar ist, aber auch keine Überbestände entstehen. Unten im Praxisteil finden Sie eine Vorlage, die Ihnen dabei hilft.
Auch Ihre Mitarbeitenden können dazu beitragen, die Prozesse zu verbessern: Sorgen Sie dafür, dass alle Mitarbeitenden die Maschinen verstehen und kleinere Probleme eigenständig beheben können. Implementieren Sie standardisierte Arbeitsanweisungen, um sicherzustellen, dass jeder Schritt im Prozess genau nach Vorgabe ausgeführt wird und so Fehler minimiert werden.
Retrofit-Maßnahmen ergreifen
Ältere Maschinen können durch modernere, energieeffizientere und produktivere Modelle ersetzt werden. Bestehende Maschinen können durch Retrofit-Maßnahmen aufgerüstet werden, um ihre Effizienz zu steigern, ohne sie komplett zu ersetzen.
Retrofit-Optionen beziehen sich auf Nachrüstungsmaßnahmen oder -lösungen, die an bestehenden Systemen, Maschinen oder Gebäuden vorgenommen werden, um deren Leistung, Effizienz, Sicherheit oder Funktionalität zu verbessern. Diese Maßnahmen steigern auch die Maschinenlaufzeit:
- Durch den Einsatz moderner Sensorik können Maschinendaten in Echtzeit überwacht und präventive Wartungsmaßnahmen eingeleitet werden, bevor es zu einem Ausfall kommt.
- Der Austausch älterer Antriebstechnologien durch energieeffiziente Motoren oder Frequenzumrichter kann die Maschinenleistung verbessern und den Energieverbrauch senken.
- Durch die Integration moderner Automatisierungslösungen (zum Beispiel speicherprogrammierbare Steuerungen, „PLCs“) kann die Maschinensteuerung verbessert werden, was präzisere und schnellere Prozesse ermöglicht.
- Die Modernisierung oder Optimierung der Software, die für die Steuerung der Maschine verantwortlich ist, kann zu einer verbesserten Performance und einem reibungslosen Betrieb führen.
- Eine benutzerfreundlichere Mensch-Maschine-Schnittstelle (Human Machine Interface, HMI) kann Bedienfehler reduzieren und die Effizienz des Maschinenbetriebs steigern.
- Durch den Einsatz von energieeffizienten Komponenten oder durch die Integration von Energiemanagementsystemen wird die Maschinenlaufzeit gesteigert, da weniger Hitze und Verschleiß entstehen.
- Die Nachrüstung mit modernen Sicherheitsfeatures (zum Beispiel: Lichtschranken, Not-Aus-Schalter, Sicherheitssteuerungen) macht nicht nur die Arbeitsumgebung sicherer, sondern minimiert auch unvorhergesehene Unterbrechungen, die durch Sicherheitsvorfälle verursacht werden.
Retrofit-Optionen steigern die Maschinenlaufzeit und sind kostengünstiger als Neuanschaffungen. Die Maschinen bleiben länger betriebsfähig; die Lebensdauer wird erhöht und die Fehler sowie Ausfälle lassen sich eher vermeiden, da die Maschinen zuverlässiger arbeiten.
Störungen analysieren
Indem Sie die Anzahl und Dauer von Störungen minimieren, steigern Sie gleichzeitig die Maschinenlaufzeit. Das folgende Excel-Tool hilft Ihnen, die Störungen zu erfassen und zu analysieren. So schaffen Sie die Grundlage zur Störgrundanalyse und zur Beseitigung der Störursachen.
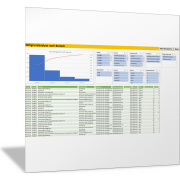
Engpässe erkennen und beseitigen
Mit den folgenden Vorlagen identifizieren Sie mögliche Engpässe und planen Maßnahmen, um die Engpässe zu beheben.
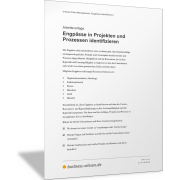
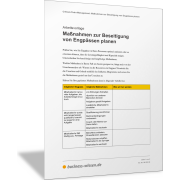
Lagerbestand überwachen
Durch die Überwachung des Lagerbestands in der Kanban-Steuerung kann eine kontinuierliche Materialversorgung sichergestellt werden, wodurch Maschinenstillstände aufgrund von Materialengpässen vermieden und die Maschinenlaufzeiten optimiert werden.
Mit der folgenden Vorlage überwachen Sie den Lagerbestand für einen ausgewählten Artikel, der nach dem Kanban-Prinzip gesteuert wird.
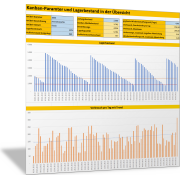
„Maschinenfähigkeit und Prozessfähigkeit berechnen“ kaufen.